당신은 주제를 찾고 있습니까 “ppg intumescent coatings – PPG PITT-CHAR NX – Next generation flexible passive fire protection“? 다음 카테고리의 웹사이트 https://ppa.charoenmotorcycles.com 에서 귀하의 모든 질문에 답변해 드립니다: https://ppa.charoenmotorcycles.com/blog/. 바로 아래에서 답을 찾을 수 있습니다. 작성자 PPG 이(가) 작성한 기사에는 조회수 3,092회 및 좋아요 18개 개의 좋아요가 있습니다.
ppg intumescent coatings 주제에 대한 동영상 보기
여기에서 이 주제에 대한 비디오를 시청하십시오. 주의 깊게 살펴보고 읽고 있는 내용에 대한 피드백을 제공하세요!
d여기에서 PPG PITT-CHAR NX – Next generation flexible passive fire protection – ppg intumescent coatings 주제에 대한 세부정보를 참조하세요
PPG PITT-CHAR NX is our next generation flexible epoxy intumescent coating system designed to resist the most severe hydrocarbon hazards – pool fires, jet fires and explosions – in both onshore and offshore environments within the oil, gas and petrochemical industries.
www.ppgpmc.com
ppg intumescent coatings 주제에 대한 자세한 내용은 여기를 참조하세요.
PPG introduces new intumescent coating
Extremely tough yet flexible, PPG PITT-CHAR NX is designed to minimise the risk of cracking and delamination during fabrication, transportation …
Source: www.hydrocarbonengineering.com
Date Published: 2/13/2022
View: 968
PPG SteelGuard – Promain
PPG STEELGUARD intumescent coating systems are specifically formulated to prove superb fire protection for civil buildings. These coatings expand at high …
Source: www.promain.co.uk
Date Published: 9/25/2022
View: 4410
주제와 관련된 이미지 ppg intumescent coatings
주제와 관련된 더 많은 사진을 참조하십시오 PPG PITT-CHAR NX – Next generation flexible passive fire protection. 댓글에서 더 많은 관련 이미지를 보거나 필요한 경우 더 많은 관련 기사를 볼 수 있습니다.
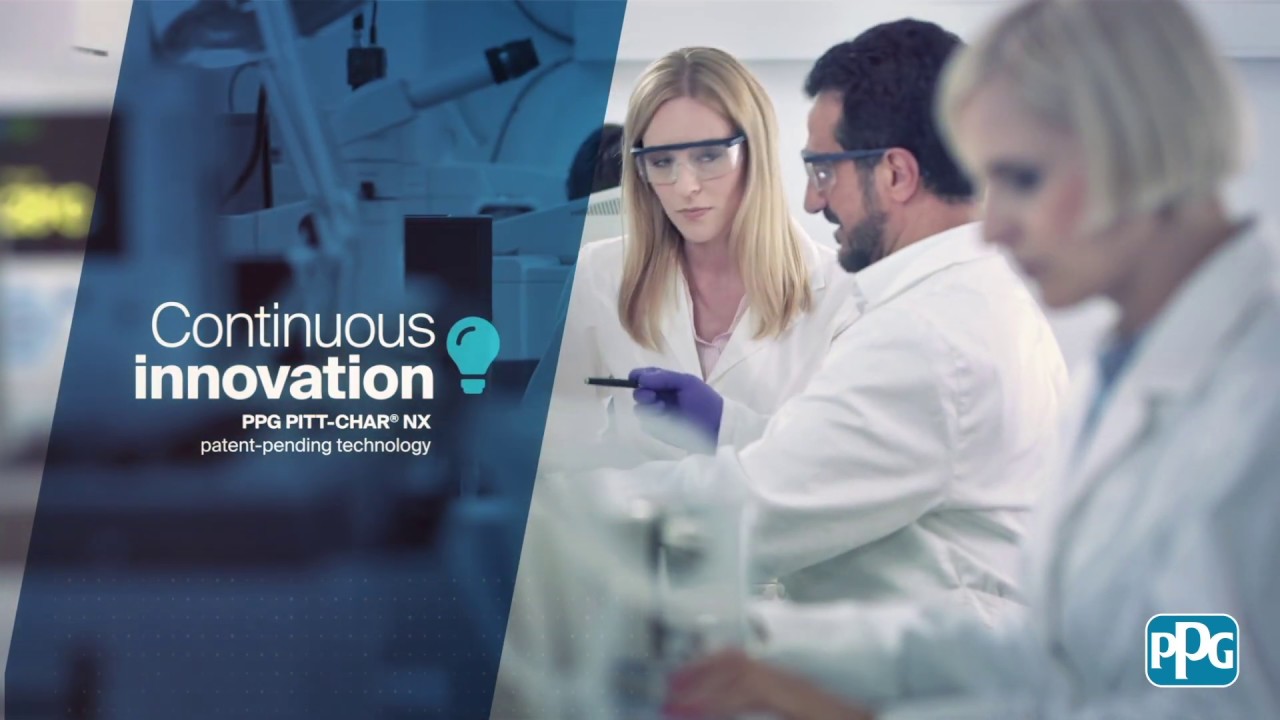
주제에 대한 기사 평가 ppg intumescent coatings
- Author: PPG
- Views: 조회수 3,092회
- Likes: 좋아요 18개
- Date Published: 2018. 12. 7.
- Video Url link: https://www.youtube.com/watch?v=b-eaxeXqfgU
What is an intumescent coating?
Intumescent paint or intumescent coatings help passively increase a building’s resistance to fire. When exposed to extreme temperatures, these coatings expand. The coatings lose density as they expand; as a result, they act as an insulator. The secret behind these coatings lies in their chemical makeup.
How much does intumescent paint cost?
As intumescent fire resistive coatings can be quite expensive ($4 to $12 per square foot, depending on the application and required rating), measuring the coating thickness can play an important role in controlling the application costs. Proper adhesion is also essential to the effectiveness of these coatings.
What is the difference between intumescent and Vermiculite?
As its name suggests, thin film intumescent fire-retardant coating provides a thinner finish compared to Vermiculite. This makes it a light material to add to the structure and its effects on a building’s stress points, overall stability and integrity are highly manageable.
How thickness is intumescent paint for 2 hour rating?
2 hours structural steel fire protection at less than 1mm thickness of an intumescent coating system.
Can you paint over intumescent coating?
Can you paint over intumescent coating? Jotun intumescent paints are usually white but they can be painted any colour with an approved topcoat. It is important to adhere to an approved paint system which is backed up by documents that you can show any inspector or building control.
How long does intumescent paint last?
The exact performance of intumescent products can vary, offering 30, 60, 90 and 120 minutes of fire resistance depending on the specific type of coating.
How thick should intumescent paint be?
Our intumescent paint is designed and tested to increase the fire performance up to 60 minutes with a thickness of paint applied of just 0.25mm or ¼ of a mm.
Where is intumescent paint required?
Intumescent Paints for Structural Fire Protection
The most common use for intumescent paint in architecture is to provide an aesthetically pleasing finish on exposed structural steel members.
How is intumescent paint applied?
Some intumescent paints are best applied using a compressed air sprayer. A compressed air sprayer is a pressurized closed system that allows the intumescent paint to be applied evenly to the entire surface.
What is vermiculite fireproofing?
1) Vermiculite is a cementious base which has been formulated to provide passive fire protection to interior elements of building construction on a variety of backgrounds, including steel, concrete, polymer-based materials, timber and advanced composite to the cellulosic fire regime.
What is vermiculite?
Vermiculite is a naturally occurring mineral (magnesium-aluminum-iron silicate) that is mined in various countries around the world, including the USA and South Africa. It gets its name from the Latin ‘vermiculare’, which means to breed worms, and the English suffix ‘ite’ which mean mineral or rock.
What is PFP in construction?
Passive fire protection (PFP), despite its name, is always at work. Based on compartmentation of fire and preventing collapse through structural fire resistance, when properly installed and maintained, your building’s passive fire protection can save lives and assets, and the building itself.
How thick is fireproofing on steel?
“Specified” Thickness of Fireproofing (SFRM)
requiring spray-on fireproofing are to have a ½″ covering of Cafco.
How much does intumescent paint expand in a fire?
Intumescent paint is applied thinly, up to 1mm, and we’ve already talked about how intumescent paint expands and swells up to 50mm when exposed to heat.
Can intumescent paint be used on wood?
Intumescent is used on many wood surfaces, including soft and hardwoods, OSB, Plywood, doors, paneling, cladding, Gypsum, and most other combustible substrates.
What are intumescent materials?
An intumescent is a substance that swells as a result of heat exposure, thus increasing in volume and decreasing in density. Intumescent materials used in fire protection will increase their volume significantly under the influence of heat (approximately at 200°C).
How do you use intumescent coatings?
- The first step of the intumescent system is the application of a compatible steel primer to the steel substrate.
- Next, the intumescent base coat is applied to the primed steel substrate to the required thickness. …
- Then, SprayFilm WB 4 / ISOLATEK Type WB 4 is coated with two coats of SprayFilm Topseal.
Where is intumescent paint required?
Intumescent Paints for Structural Fire Protection
The most common use for intumescent paint in architecture is to provide an aesthetically pleasing finish on exposed structural steel members.
How does intumescent coating protect steel?
Intumescent coatings provide one such method. They react in the presence of intense heat to form an insulating layer, protecting the underlying steel and extending the duration of its structural integrity.
Intumescent Paint: Everything You Need To Know
What Is Intumescent Paint?
When you’re responsible for a fire management strategy, every choice matters. One step you can take to add fire resistance to your facility is using intumescent paint.
But what is intumescent paint, exactly?
Intumescent paint or intumescent coatings help passively increase a building’s resistance to fire. When exposed to extreme temperatures, these coatings expand. The coatings lose density as they expand; as a result, they act as an insulator.
The secret behind these coatings lies in their chemical makeup. An intumescent coating consists of many chemicals, all suspended in a binder. The binder softens in response to heat exposure, letting the suspended chemicals react. These chemicals produce a foam, which hardens into an insulating material called “char.”
Intumescent Paint vs. Cementitious Paint
Intumescent coating is one of three major choices for passive fire protection. The other categories in this field are dense concrete and lightweight cementitious fireproofing. Keep reading to understand the difference between intumescent and cementitious paint.
Lightweight cementitious coatings are cement-based products used to fireproof structures. Like intumescent paint, these coatings can stand up to very hot temperatures. As their name implies, they are much lighter than dense concrete.
That said, cementitious coatings have some notable drawbacks. One major problem – space between the substrate and the coating will develop over time. That space can become filled with moisture, encouraging corrosion. As a result, these coatings can end up weakening the substrate.
Cementitious coatings also have high costs of installation and a tendency to crack. Because of these issues, cementitious coatings have lost popularity over time. Instead, intumescent fireproofing has become the go-to option for fire retardant paint today.
Unsure about the whether cementitious or intumescent coatings are right for your project? Consult one of our industrial coating partners today!
How Much Does Intumescent Paint Cost?
There’s both a short answer and a long answer to this question, but we’ll start with the long answer. Intumescent paint costs for your project can vary based on many factors. These factors include:
Coating thickness
Adhesion
Required surface preparation
Environmental resistance
Expansion ratio (that is, how much a coating expands when exposed to high temperatures)
VOC levels
With all that in mind, you can expect to pay anywhere from $4 to $12 per square foot of intumescent paint. The exact amount you’ll pay will depend on the factors listed above, among others. Still, it should be somewhere in that ballpark.
Need to brush up on your industrial coating basics? Check out our complete guide here.
We’ve partnered with top-rated intumescent paint suppliers that can help you save big. Get a free consultation and talk with a qualified expert today.
Intumescent Paint Fire Ratings
There are lots of fire ratings out there, but which intumescent paint fire rating should you focus on? Two fire ratings are important to know about for intumescent fireproofing: ASTM E84 and ASTM E119.
ASTM E84
One important intumescent paint fire rating is American Society for Testing and Materials (ASTM) Test Method E-84, or “ASTM E84” for short. This rating focuses on a material’s flame-spread.
In ASTM E84 tests, a 20-inch by 25-foot material sample is installed on a test chamber’s ceiling. Testers then apply a gas flame to one end of the sample. The results of this test determine the material’s flame spread rating (FSR) on a scale of 0-200. Inorganic reinforced cement board has a rating of zero on this scale, while red oak has a rating of 100.
From there, materials fall into three classes. Class A materials have FSRs of 0-25, Class B materials have FSRs of 26-75, and Class C materials have FSRs of 76-200.
ASTM E119
While ASTM E84 deals with flame-spread, ASTM E119 is all about how long a material can deal with fire. For intumescent paint, “2 hour rating” and phrases like it may refer to this test.
For ASTM E119 testing, a material sample is exposed to a temperature-controlled fire. This test measures the reliability of structural elements like:
Bearing walls
Partitions
Columns
Floors
Roofs
Beams
Protective membranes
In the next section, we’ll recommend intumescent paints or steel and wood. This video provides an excellent primer too how intumescent works on these types of materials.
Intumescent Paint For Steel
Summary: This Carboline product is a solvent-based intumescent paint that protects interior structural steel. It’s well-suited for use with interior steel beams, pipes, and columns.
Product features:
Durable, dust-free surface
Good-looking smooth finish
Compliant with VOC requirements
Fire rating: Up to four hours, depending on the structure users apply it to.
Product data sheet available for download here. For more about Carboline, read our review of Carboline’s most popular products.
Summary: From Sherwin-Williams’ Firetex brand, this intumescent coating is a water-based option. It’s great for exposed structural steel in interior settings.
Product features:
Paint-like finish
Resistant to impact
Applies well to substrates
Fire rating: Up to two hours fire protection.
Product data sheet available here.
Summary: PPG’s STEELGUARD line helps protect steel substrates from cellulosic fires. This coating is a one-component, solvent-borne coating created with structural steelwork in mind.
Product features:
Apply on-site or off-site
Weather-resistant for up to a year
Matte finish
Fire rating: Up to 150 minutes cellulosic fire protection.
Product data sheet available here.
Intumescent Paint For Wood
Summary: Flame Seal Products, Inc., a company specializing in fire-resistant coatings, sells this coating. It has a lower activation temperature than other intumescent paints – use it with wood or plastic.
Product features:
Clear coating
Safe to handle
Easy to apply
Fire rating: Provides Class A or Class B protection when applied correctly.
Product data sheet available here.
Summary: A Shield Industries, Inc. product, this water-based coating can protect a wide variety of substrates. The materials it’s compatible with include wood, steel, and many others.
Product features:
Low VOC levels
Durable, decorative finish
Thin film coating
Fire rating: Tested to various fire resistance standards. Up to two hours fire protection when applied to a heavy steel column.
Product data sheet available here.
Summary: International Fireproof Technology, Inc. sells intumescent paints that can help boost your structure’s fire resistance rating. This water-based intumescent coating is especially suited for use with wood and gypsum.
Product features:
Apply with spray, roll, or brush
Non-toxic and hypoallergenic
Flat finish
Fire rating: Provides Class A fire protection in accordance with ASTM E84. Can protect combustible substrates from fire for up to 30 minutes.
Product data sheet available here.
Related article: Best Fire Resistant & Fire Retardant Paints in 2022
How to Measure Intumescent Fire Resistive Coating Thickness
Updated: 12/10/2021
DeFelsko offers many models of the PosiTector 6000 thickness gage that are ideal for measuring the total thickness of intumescent fire resistive coatings (IFRM). Selection is primarily dependent on the expected coating thickness.
What are Intumescent Fire Resistive Coatings?
Intumescent fire resistive coatings are applied to steel building supports such as beams, channels, pipes and tubular columns to protect their structural integrity in fires. DeFelsko manufactures hand-held, non-destructive coating thickness gauges that are ideal for measuring the dry film thickness of these coatings. Additionally, dew point meters are available for ensuring that they are applied under ideal environmental conditions.
Although steel does not burn, it can be severely weakened when exposed to high temperatures for extended periods, such as in a building fire. It is believed that such damage led to the collapse of the World Trade Centre towers. Since the attacks of 9/11, greater attention has been focused on the development and application of better and more durable intumescent coatings.
When exposed to fire, an intumescent coating generally expands in thickness by 15 to 30 times in a standard test1, forming a thick layer of foam that protects the steel by thermally insulating it from the heat. Some manufacturers report expansions as great as 100 times for unspecified conditions2. As part of the expansion process, most coatings generate an outer ash-like char layer. As the fire continues, the ash coating erodes, exposing the remaining intumescent coating to form more char. Depending on the coating thickness, this process repeats itself several times.1
Intumescent fire resistive coatings generally require a primer for adherence. A decorative/protective topcoat may also be necessary—especially in humid environments. A reinforcing mesh can be used to better retain the char layer on certain shapes.
Measurements Key to Quality Assurance
The effectiveness of an intumescent fire resistive coating depends on the coating thickness and its ability to retain the ash layer. Coating thickness typically ranges from 30 to 500 mils (0.8 to 13 mm). The applied thickness must meet the product specifications for the type of structure being coated and the applicable building code requirements (e.g., to withstand a fire of a certain temperature and duration).
As intumescent fire resistive coatings can be quite expensive ($4 to $12 per square foot, depending on the application and required rating), measuring the coating thickness can play an important role in controlling the application costs.
Proper adhesion is also essential to the effectiveness of these coatings. As the adhesion is strongly affected by the climatic conditions at the time of application, manufacturers generally specify the range of conditions for which their products may be applied—e.g., relative humidity, air temperature, and the difference between the surface and dew point temperatures.3, 4 Therefore, it is important to carefully monitor the climatic conditions when applying intumescent coatings.
DeFelsko manufactures gages that are ideally suited for measuring the thickness of intumescent fire resistive coatings, testing coating adhesion, and for monitoring the humidity and temperature when they are applied.
DeFelsko’s Intumescent Dry Film Thickness Measurement Solution
DeFelsko offers many models of the PosiTector 6000 Coating Thickness Gage that are ideal for measuring the total thickness of intumescent fire resistive coatings. Selection is primarily dependent on the expected coating thickness.
The PosiTector 6000 FT series are ideal for measuring coating thickness up to 250 mil (6.4 mm). These gages provide results with a maximum accuracy of ± 0.5 mil (0.01 mm) + 1% of reading for measurements less than 100 mil (2.5 mm). For readings over 100 mil (2.5 mm), the accuracy is ± 0.5 mil (0.01 mm) + 3% of the reading.
The PosiTector 6000 FKS series is recommended for thicker applications up to 500 mil (13 mm), for which the gages provide results with an accuracy of ± 1 mil (0.02 mm) + 3% of the reading.
The PosiTector 6000 FLS series is available for very thick applications up to 1.5 inches (38 mm), with an accuracy of + 0.01 in. (0.2 mm) + 3% of the reading.
Downloading the measurements from the PosiTector 6000 is as seamless as storing it to a USB data stick or connecting a USB cable to a computer. These features allow for convenient printing and further analysis on a PC. The data logging and downloading capabilities allow an operator to easily track variations in coating thickness through multiple measurements over large areas. The Advanced models come with wireless WiFi and Bluetooth® connections. See our PosiSoft Solutions page for more information.
A detailed brochure can be downloaded here.
PosiTector 6000 Complies with Fireproofing Industry Best Practice
The use of PosiTector 6000 gages to measure intumescent coating thickness complies with accepted industry best practice. The National Fireproofing Contractors Association5 publishes a quality assurance procedure for the application of intumescent coatings.6 This procedure requires that the “final thickness must be measured with a dry film thickness gauge in accordance with AWCI [Association of the Wall and Ceiling Industry7] Technical Manual 12-B, ‘Standard Practice for the Testing and Inspection of Field Applied Thin-Film Intumescent Fire-Resistive Materials; an Annotated Guide.8 ”
While the AWCI guide notes that coating thickness measurements should be made with a gage approved by the building authority having jurisdiction, it lists only two acceptable measurement techniques: magnetic pull-off gages and magnetic flux-based sensors. The PosiTector 6000 gages use the latter accepted approach.
With reference to the AWCI guide, at least one intumescent coating manufacturer (A/D Fire Protection Systems) lists DeFelsko as a manufacturer of suitable dry film gages for measuring coating thickness.8
Monitoring Environmental Conditions Prior to Intumescent Paint Application
As noted above, intumescent fire resistive coatings should only be applied under ideal ranges of relative humidity and temperature.
The PosiTector DPM Dew Point Meter measures and records climatic conditions including: relative humidity, air temperature, surface temperature, dew point temperature and the difference between surface and dew point temperatures.
The PosiTector DPM is capable of recording the following environmental parameters: the % relative humidity (%RH), ambient air temperature (Ta), surface temperature (Ts), dew point temperature (Td), and surface temperature minus dew point temperature (Ts-Td). All five of the climatic conditions are monitored and calculated at the same time and, at the press of a button, the readings can be stored in memory along with the date and time. The PosiTector DPM also has a unique auto logging feature that automatically records datasets containing all 5 climatic conditions at a user-selected time interval. This is useful for maintaining a complete record of environmental conditions and trends leading up to, during, and after the application of an intumescent coating.
Free Consultation
For current pricing or to order these instruments, please contact us by e-mail at [email protected], by telephone at (315) 393-4450 or by fax at (315) 393-8471. If you require additional technical information or have questions relating to your particular application, we encourage you to take advantage of our years of experience in recommending the best gage for your needs.
References
1. https://www.ul.com/news/mastic-and-intumescent-coatings
2. https://www.nullifire.com/en_GB/our-solutions/intumescent-coatings/
3. https://multimedia.3m.com/mws/media/373703O/3m-firedam-spray-200-flyer-technical-data-sheet.pdf
4. https://www.adfire.com/products/ (select a product, then “Product Data Sheet”)
5. The NFCA represents contractors that install passive fireproofing products to building structures and manufacturers of the products (www.nfca-online.org). The association provides a training program for special inspectors who desire to learn proper inspection and test procedures for the inspection of … intumescent materials applied to structural steel members. (https://www.nfca-online.org/certifications/ul-qualified-contractor.asp)
6. https://www.nfca-online.org/NFCA%20400%20Final%20052308.pdf
7. The AWCI represents over 2,200 companies and organizations involved in a variety of building systems – including fireproofing (www.awci.org).
8. The AWCI guide is available by ordering through: https://awci.force.com/portal/s/store#/store/browse/tiles
Fire Retardant Coatings
Fire retardants are nothing new in construction. Since the ‘70s fire retardant coatings and materials such as Vermiculite have been used on buildings to protect the steel from fire. With an appearance similar to paper mache everyone has likely seen this type of protective coating in car parks, or even older sporting arenas.
With the advances of technology, however, newer alternatives are available including thin-film intumescents. And whilst we will be the first to admit that Vermiculite will always have a place (for non exposed areas), when it comes to architectural finishes, thin-film coatings cannot be beaten.
So what are the differences of thin film options (sometimes incorrectly called intumescent fireproofing paint)? This blog aims to find out.
Why It Is Time to Move on from Vermiculite
Vermiculite is a product that has been around for more than 30 years now. One of the reasons why it became a popular fire retardant is because it often comes in spray form, which is easy to apply to structures. Plus, it is affordable in terms of cost per meter. However, this technology has barely changed over the years and is essentially outdated. Further, as mentioned above, when it comes to exposed steel (which is the way building trends have gone), vermiculite is an eye-sore as it cannot be top coated and it takes up a lot of space.
Further, whilst it may be quicker to apply vermiculite, the time to dry is much longer, and the risk of damage, much higher, meaning the initial savings may be quickly eroded.
Compared to current intumescent fire retardant coating technologies, Vermiculate spraying means waiting for it to dry. This will restrict builders’ access to certain floors which will affect the construction timeline. And while it is a good material to passively protect a building from fire, Vermiculite is surprisingly susceptible to damage.
In fact, it can easily be corroded by water. Since it easily absorbs moisture, Vermiculite can end up cracking, thus compromising the integrity of the structure and the effectiveness of a building’s overall fire protection. That makes it unsuitable for use on exterior parts of a building, perimeter structures, and other areas exposed to inclement weather.
On top of all that, Vermiculite can negatively impact a building design’s aesthetics. Many architects and engineers don’t like to specify it as it can be downright ugly. Since Vermiculite is a thick material, it can limit construction clearances, which leads to the reduction of available open space. The thickness also adds more weight to the structure, which needs to be carefully managed otherwise a building’s stability and integrity can be compromised.
What are we saying you ask? Basically, it is high time to move on to better fire-retardant coating alternatives. This is where intumescent fire retardant paint comes into the picture.
Intumescent Fireproofing Paint – Why Switch to Them?
Intumescents are the latest in fire protection technology – yet they are far from “new”. There are several options out there, but generally, they are composed of a primer, basecoat, and sealer coat. They contain substances that produce non-flammable gasses when coming into contact with fire, inhibiting the spread of flames. They also swell into thick padding (called a char), which will provide insulation and protection from a conflagration.
As mentioned, there are various options for intumescent fireproofing paint out there that can meet different fire resistance requirements. Whether a building is required to meet the 30, 60, or 90 minutes fire resistance requirement, intumescents can potentially be used. In fact, recent developments have made available coatings that can withstand fire for up to 120 minutes. This can really help minimise the damage just in case it takes longer to control a fire accident.
Thin Film Intumescents Are the Way Forward
It makes sense to employ the latest and more effective fire retardant technologies on today’s construction projects. Thin film intumescent fireproofing paint is especially a great option. Here are the main reasons why:
Thin Film Is Thin and Light
As its name suggests, thin film intumescent fire-retardant coating provides a thinner finish compared to Vermiculite. This makes it a light material to add to the structure and its effects on a building’s stress points, overall stability and integrity are highly manageable. It is also great for use in tighter spaces and won’t reduce available spaces much.
As already mentioned above, thin film does well – up to 7x its original thickness when coming into contact with fire. It is designed to protect underlying structure, which thus mitigates the malevolence and spread of a fire.If nothing else, this makes it a highly effective and reliable intumescent fire retardant paint.
More Design and Aesthetics Freedom – Outdoor Use
Since it is light, thin film intumescent paint provides architects with more versatility to design more aesthetically pleasing structures. Plus fire rated Intumescents for concrete, timber and steel are all available
Intumescent paint for steel is the most commonly used option given the prevalence of steel in construction still, though with the rise of timber products for construction, this balance will change. But in saying that it will change to more Intumescents for timber and less vermiculite overall.
It Dries Faster
You don’t have to wait for too long for thin film to dry. It can be top-coated as well. So, whilst it can be more expensive to apply you will be able to save on the man-hours required to fireproof a building. Plus, other construction timelines will only be affected minimally – if at all.
Thin Film Can Be Applied Offsite
The fact that thin film intumescent fireproofing paint can be applied offsite makes it an even better fire protection choice. Any parts or steel that needs to be coated can be processed at a different location while more work can continue on the main construction time.
After the paint coating is done offsite, the finished parts can be transported and installed into the building without fuss. And as intumescents such as Nullifire are resilient and harder to damage, the risks in moving the steel is minimized. Again, this provides more flexibility in how a building is designed and constructed.
That also means that the mess and disruption on the main construction site are reduced. Basically, using thin film is great not only for fire protection but also for productivity.
Conclusion
When it comes to fireproofing a structure, Vermiculite may be a cost-effective option at first glance but a thin film intumescent fire retardant coating is a far better option.
It is more effective, it provides design flexibility, and will improve the flow of the overall construction process.
2 hours structural steel fire protection at less than 1mm thickness of an intumescent coating system
Interchar 1260 A next generation water based intumescent coating system for commercial structural steel fire protection is now available in Australia.
This system has the potential for up to 2 hours protection at less than 1mm dft.
A cost effective solution with a complete AS1530.4 / AS4100 documented system from one manufacturer, primer, intumescent and topcoat if required, ensuring single point supply.
Please feel free to contact myself or your local International Paint technical representatives for any additional information and assistance
PPG introduces new intumescent coating
Specialist industrial fire resistant coatings, commonly referred to as ‘fireproofing’ or Passive Fire Protection (PFP) are complex products that must perform a difficult task: providing consistent protection and durability in extreme environments, while also delivering in terms of total lifecycle cost.
Coatings end users in the onshore and offshore energy and petrochemical industries have varying requirements but all need products certified to international standards that can provide the required level of safety.
It is a market subject to strong price competition with many apparently similar products available. This makes understanding the stakeholders and their requirements all the more important in supplying the right product.
Understanding the value chain
At the top of the value chain are the owner-operators (the end-users if there is a fire) whose principal desire is a safe solution. They are concerned with price, but this comes in the context of durability and minimising the need for maintenance across an asset’s lifecycle that could be 20 years or more. If operating offshore they are also very interested in a high quality, durable coating with lighter applied weight.
Next is the engineering, procurement and construction (EPC) contractor who has a shorter period of liability – perhaps as little as five years – and is looking to meet client requirements for performance against a stronger competitive incentive. Finally, where the coating meets the steel are the fabricator and the applicator, sub-contractors who are interested in which coating system will be fastest to apply to the specified quality level and target price.
The stakeholders in the supply chain – whether asset owners, engineers, fabricators or contractors – all need to be aware that while some coatings appear designed (and some are certified) to resist all potential fire hazards, they may in fact only be suitable for pool fires rather than jet and pool fires; a critical difference in selecting a coating that is likely to face both scenarios.
Most intumescent coatings developed in recent years still rely on a rigid formulation and as a result, many may not perform as well as expected in practice when the steelwork moves either mechanically or with change in temperature. They can also be prone to delamination and cracking, so offer very limited integrity. The industry standard has moved on to use of an insulation system that slows the rate of heat-up and buys additional time for rescue or evacuation.
Creating better products
For over 35 years, PPG’s PITT-CHAR technology has been trusted to safeguard personnel and equipment in hazardous environments around the world.
In considering the development of the next generation of intumescent coating, PPG set out to develop a coating system that was safer, tougher, thinner, lighter and faster to apply. PPG PITT-CHAR NX draws on the heritage of the original PITT-CHAR product but has an entirely new formulation based on a fresh research and development cycle. The aim of this was to bring increased value to the customer.
As a result, PPG has developed a unique product with the flexibility required by the industry, which also offers the additional properties of thinness and lightness. PPG PITT-CHAR NX works equally well in onshore and offshore environments with no drop in performance after as much as 20 years exposure. Because the coating is thinner in application, less volume is required but it is still resistant to pool fires and jet fires so can be safely used in either situation with little or no additional material thickness.
Changing standards in coatings certification were also a driver to developing PITT-CHAR NX. In particular, PPG wanted a new coating that was compliant with the latest environmental exposure and fire standards including NORSOK M501 Rev 6, UL2431, UL1709 Rev 5 and BS 476 hydrocarbon fires with ISO 22899-1 jet fire – for all types and sizes of structural steel and safety-critical equipment.
PPG PITT-CHAR NX is also tested to the International Maritime Organization’s FTP Code and the latest ISO 20902 standard for hydrocarbon fire-rated divisions such as decks and bulkheads.
High performance
Globalisation and lower oil and gas prices have put pressure on project costs leading to a rise in off-site modular or stick-built fabrication techniques. While this is generally more cost-effective, it does add unique challenges for PFP coatings.
Before they are assembled on-site, pre-fabricated coated steel often travels long distances, sometimes across continents, and in vastly varying climatic conditions. Any damage to the PFP coating can impact its ability to perform effectively when the structure is in service or result in expensive repairs and potential delays to start-up.
Extremely tough yet flexible, PPG PITT-CHAR NX is designed to minimise the risk of cracking and delamination during fabrication, transportation and construction. This toughness provides dependable performance against weathering and excellent corrosion protection throughout the asset’s entire lifetime.
Once installed and when exposed to the high temperatures of the fire, PPG PITT-CHAR NX expands to form a robust, insulating char that significantly reduces the speed of at which the protected item heats up.
The insulation maintains steel integrity, and hence buys crucial time for personnel to escape and equipment to function on demand.
By utilising the carbon fibre PPG PITT-CHAR® CF mesh, it was possible to significantly improve the system’s fire resistance performance making it thinner, lighter and faster to apply than alternative systems.
The incorporation of the carbon fiber mesh not only produces substantial savings, but turns the coating system into a composite, greatly enhancing its toughness and improves the crack and damage resistance throughout all phases of the project, making the system even safer and tougher under extreme environmental and accidental load conditions.
Flexible fire protection
Some intumescent coatings are designed and marketed towards onshore fire protection applications and as such, are designed to tackle less aggressive pool fires. A coating designed for more aggressive jet fires will normally require a more robust material and additional thicknesses due to the erosive forces it generates.
PPG PITT-CHAR NX is unique in providing class-leading loadings and the flexibility to tackle jet and pool fires, whether onshore or offshore in oil, gas or petrochemical applications. For PPG customers this means they have the assurance that a single product provides the protection for either situation with little or no additional material, thereby providing a safer solution. Lightness of the coating is an advantage where weight is important, whether in moving steel components or in an offshore application. PITT-CHAR NX can help significantly in reducing both transport and construction costs.
The previous generation of PITT-CHAR had a typical application thickness of 12 mm for 2 hr pool fire protection. Competing coatings are now at 10 mm but PITT-CHAR NX has moved the bar to less than 8 mm for the same scenario.
Faster results recognised
Product lightness also translates into less product to apply, but in addition PITT-CHAR NX has been formulated to cure in a unique way allowing a saving of 60% in application time. A three to four day application process could be reduced to one day and the steel can be moved only a few hours after application. The enhanced environmental performance was also achieved without a topcoat, so further savings on material and application time can be realised.
Written by Peter Scott, PPG Protective and Marine Coatings.
PPG STEELGUARD 651 Intumescent coating
The following PPG and Johnstone’s Trade topcoats are approved for use over PPG STEELGUARD™ 651 at an applied DFT of 50 μm for internal environments only. Johnstone’s Trade Steel and Cladding Semi-Gloss topcoat. Johnstone’s Trade Aqua Waterbased Satin or Gloss. PPG AQUACOVER 45.
PPG Steelguard the Superior Intumescent Cellulosic Fire Protection Paint Solution
About PPG SteelGuard
PPG STEELGUARD intumescent coating systems are specifically formulated to provide superb fire protection for civil buildings. These coatings expand at high temperatures from a thin coating into a thick, foam-like layer that insulates the steel from the fire; this insulation maintains the steel’s stability, providing vital time to help people escape. These coatings produce an extremely smooth surface that can be topcoated with a variety of colors. The range also includes waterborne coatings specifically designed for onsite use, conforming to the most stringent environmental regulations, applicable even while people are using the building.
The PPG STEELGUARD range of products have European (EN 13381) and national certification from many countries.
Cellulosic Fire Protection
PPG STEELGUARD
Formulated to expand and creating an insulating char when exposed to fire, STEELGUARD coatings maintain the steels stability, providing up to 120 minutes of fire protection – saving lives and limiting asset damage.
The STEELGUARD range includes water based and solvent based solutions for off-site and on-site application to I sections, circular and rectangular hollow sections.
PPG STEELGUARD 651 Waterborne Intumescent
Buy time, save lives and limit asset damage with w
A circular column with STEELGUARD™ 651 coating shows after testing that the char has kept the steel fully encapsulated.
In-house test specimen application of STEELGUARD™ 651 intumescent coating by PPG
PITTSBURGH, May 16, 2016 – PPG’s (NYSE: PPG) protective and marine coatings business has introduced STEELGUARD™ 601 and STEELGUARD 651 waterborne thin-film intumescent coatings, which minimize environmental impact and deliver up to 120 minutes of cellulosic fire protection.
The new STEELGUARD waterborne range by PPG is formulated to reflect modern building design, where structural steel demands high performance from a protective coating system. In addition to a smooth and aesthetically pleasing finish that protects the structure against corrosion, coatings must also maintain the steel’s stability in the event of a fire.
These highly protective intumescent coatings are designed to expand at high temperatures, from a very thin, lightweight film into a thick foam-like layer that forms an insulation char protecting the steel from cellulosic fire. The heat insulation properties of these coatings maintain the steel’s stability, providing up to 120 minutes of fire protection at temperatures ranging from 350 C (660 F) to 750 C (1380 F).
“PPG has worked closely with architects and designers around the world, and we understand the pressures to specify ‘greener’ products which are also highly effective in maintaining structural stability,” said Jason Wall, PPG global cellulosic passive fire protection (PFP) manager. “By investing in research and development of this waterborne intumescent technology that contributes to a greener and safer environment, we can also buy additional time for people to escape and firefighters to arrive, saving lives and limiting damage to buildings and assets.”
STEELGUARD 601 and STEELGUARD 651 single-pack waterborne coatings have a high volume of solids, very low levels of volatile organic compounds (VOCs) and low odor, thus providing a healthier atmosphere for workers. These benefits should enable application to take place while the building is in use or still under construction with minimal disruption to other on-site installers.
Both coatings have been tested and certified to the latest international standards and comply with the most stringent environmental regulations, such as EN 13381-8:2013 and BS476 Parts 20/21. They also meet requirements for ISO 12944-2 C1* and C2 internal environments and ETAG 018-2 Z2* and Z1 and Y durability categories.
To ensure that designers and contractors can make full use the coatings, PPG engineers are available globally to provide expertise in intumescent fire protection and advise on the relevant industry standards and fire ratings. PPG has the engineering capability to support clients in the early stages of development, guiding them through the specification process and providing support through to project completion and beyond.
PPG: WE PROTECT AND BEAUTIFY THE WORLD™
At PPG (NYSE: PPG), we work every day to develop and deliver the paints, coatings and materials that our customers have trusted for more than 130 years. Through dedication and creativity, we solve our customers’ biggest challenges, collaborating closely to find the right path forward. With headquarters in Pittsburgh, we operate and innovate in more than 70 countries and reported net sales of $15.3 billion in 2015. We serve customers in construction, consumer products, industrial and transportation markets and aftermarkets. To learn more, visit www.ppg.com.
We protect and beautify the world is a trademark and the PPG Logo is a registered trademark of PPG Industries Ohio, Inc.
STEELGUARD is a trademark of the PPG Group of Companies.
PPG Media Contact:
Marielle van der Linden
Protective and Marine Coatings
+31 20 407 5273
ppgpmc.com
키워드에 대한 정보 ppg intumescent coatings
다음은 Bing에서 ppg intumescent coatings 주제에 대한 검색 결과입니다. 필요한 경우 더 읽을 수 있습니다.
이 기사는 인터넷의 다양한 출처에서 편집되었습니다. 이 기사가 유용했기를 바랍니다. 이 기사가 유용하다고 생각되면 공유하십시오. 매우 감사합니다!
사람들이 주제에 대해 자주 검색하는 키워드 PPG PITT-CHAR NX – Next generation flexible passive fire protection
- PPG
- PITT-CHAR
- NX
- PITT-CHAR NX
- Intumescent
- Protective
- Coating
- Hydrocarbon
- Flexible
- Epoxy
- Passive
- Fire
- Protection
- PFP
PPG #PITT-CHAR #NX #- #Next #generation #flexible #passive #fire #protection
YouTube에서 ppg intumescent coatings 주제의 다른 동영상 보기
주제에 대한 기사를 시청해 주셔서 감사합니다 PPG PITT-CHAR NX – Next generation flexible passive fire protection | ppg intumescent coatings, 이 기사가 유용하다고 생각되면 공유하십시오, 매우 감사합니다.