당신은 주제를 찾고 있습니까 “przykładowa ocena ryzyka maszyny – Odc. 6: Procedura oceny zgodności – dokumentacja techniczna, ocena ryzyka, badania i testy“? 다음 카테고리의 웹사이트 https://ppa.charoenmotorcycles.com 에서 귀하의 모든 질문에 답변해 드립니다: https://ppa.charoenmotorcycles.com/blog. 바로 아래에서 답을 찾을 수 있습니다. 작성자 parpgovpl 이(가) 작성한 기사에는 조회수 1,827회 및 295104 Like 개의 좋아요가 있습니다.
przykładowa ocena ryzyka maszyny 주제에 대한 동영상 보기
여기에서 이 주제에 대한 비디오를 시청하십시오. 주의 깊게 살펴보고 읽고 있는 내용에 대한 피드백을 제공하세요!
d여기에서 Odc. 6: Procedura oceny zgodności – dokumentacja techniczna, ocena ryzyka, badania i testy – przykładowa ocena ryzyka maszyny 주제에 대한 세부정보를 참조하세요
Szkoła dla eksportera – Oznakowanie CE – czyli unijne dyrektywy nowego i globalnego podejścia.
Dokumentacja techniczna produktu. Ocena ryzyka. Proces zmniejszania ryzyka. Praktyczne informacje na temat badań.
Zobacz również prezentację w pdf na stronie Enterprise Europe Network – http://www.een.org.pl/index.php/Szkola_dla_eksportera/articles/szkola-dla-eksportera-oznakowanie-CE.html..
przykładowa ocena ryzyka maszyny 주제에 대한 자세한 내용은 여기를 참조하세요.
Ocena ryzyka przy projektowaniu maszyn wg dyrektywy 2006 …
Tak więc konieczność prowadzenia oceny ryzyka przez projektanta maszyny … wypełnione. Przykład wykazu zentyfikowanych zagrożeń pokazany jest na rys. 5.
Source: archiwum.ciop.pl
Date Published: 6/2/2022
View: 1459
Rola i znaczenie oceny ryzyka w procesie budowy maszyn
Wg dyrektywy maszynowej 2006/42/WE, producent maszyny lub jego upoważniony przedstawiciel musi zapewnić przeprowadzenie oceny ryzyka w celu …
Source: bezpieczenstwowsystemachsterowania.pl
Date Published: 2/9/2021
View: 581
8 kroków do bezpiecznej maszyny – Od oceny ryzyka do …
Krok 1: Ocena ryzyka jako klucz do bezpieczeństwa maszyn … Koncepcja bezpieczeństwa uwzględnia na przykład wykorzystanie stałych i …
Source: automatykab2b.pl
Date Published: 4/25/2021
View: 8081
Ocena ryzyka maszyn – Pilz PL
Ocena zagrożeń zgodnie z Dyrektywą Maszynową: Dzięki ocenie ryzyka Pilz | Twoi eksperci ds. bezpieczeństwa maszyn | Dowiedz się więcej już teraz!
Source: www.pilz.com
Date Published: 12/6/2021
View: 569
OCENA I REDUKCJA RYZYKA TECHNICZNEGO MASZYN
Zaprezentowano przykładowe, proponowane metody oceny dla wybranej maszyny – według firm Elokom oraz Siemens. W artykule zawarto wybrane fragmenty i dane z …
Source: www.ptzp.org.pl
Date Published: 9/26/2021
View: 9461
ocena ryzyka maszyny wg dyrektywy MAD 2006/42/WE – IKMJ
Dyrektywa maszynowa MAD 2006/42/WE nie wymaga przekazywania dokumentacji dotyczącej oceny ryzyka wraz z maszyną, ale musi ona być przechowywana …
Source: ikmj.com
Date Published: 3/13/2021
View: 1210
Analiza, ocena i ewaluacja ryzyka maszyn – CE Solution
Przeprowadzanie audytów bezpieczeństwa maszyn (analiz i oceny ryzyka), … Przykładowe strony raportu analizy, oceny i ewaluacji ryzyka dla maszyny.
Source: www.ce-solution.pl
Date Published: 8/22/2022
View: 1201
Po bezpiecznej stronie, czyli jak oszacować ryzyko …
Dzisiaj zajmiemy się 1 punktem, czyli oceną ryzyka. … Przykład: projektujemy maszynę, która zgodnie z założeniami ma pracować w hali …
Source: wagodirect.pl
Date Published: 7/29/2022
View: 248
주제와 관련된 이미지 przykładowa ocena ryzyka maszyny
주제와 관련된 더 많은 사진을 참조하십시오 Odc. 6: Procedura oceny zgodności – dokumentacja techniczna, ocena ryzyka, badania i testy. 댓글에서 더 많은 관련 이미지를 보거나 필요한 경우 더 많은 관련 기사를 볼 수 있습니다.
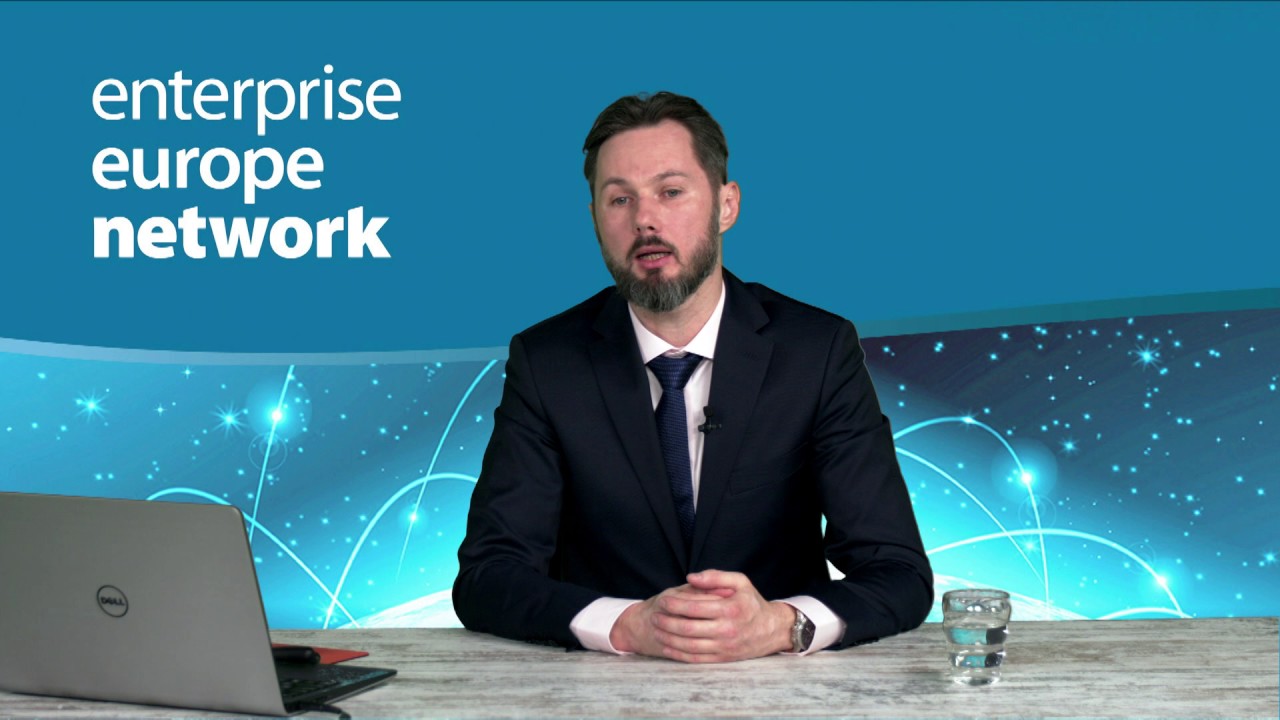
주제에 대한 기사 평가 przykładowa ocena ryzyka maszyny
- Author: parpgovpl
- Views: 조회수 1,827회
- Likes: 295104 Like
- Date Published: 2017. 1. 18.
- Video Url link: https://www.youtube.com/watch?v=310558Uznek
Na czym polega ocena ryzyka przeprowadzana przez producenta maszyn?
pracodawca ocenia i dokumentuje ryzyko zawodowe związane z wykonywaną pracą oraz stosuje niezbędne środki profilaktyczne zmniejszające ryzyko. Pracodawca informuje pracowników o ryzyku zawodowym, które wiąże się z wykonywaną pracą, oraz o zasadach ochrony przed zagrożeniami.
Na czym polega ocena ryzyka?
Ocenę ryzyka zawodowego można rozumieć jako dokładne sprawdzenie i ocenę, co w miejscu pracy może zaszkodzić lub wyrządzić krzywdę pracownikom. Dzięki niej można zweryfikować czy zastosowano wystarczające środki ograniczające lub eliminujące zagrożenia oraz określić, co należy jeszcze zrobić, aby do tego doprowadzić.
Co to jest dyrektywa maszynowa?
Dyrektywa maszynowa stanowi zbiór wymagań zasadniczych stawianych producentom maszyn. Producent musi zapewnić, że maszyna wprowadzona po raz pierwszy na rynek Europejskiego Obszaru Gospodarczego (EOG) spełnia wymagania zasadnicze opisane w dyrektywie maszynowej 2006/42/WE.
Jak zrobić mapę ryzyka?
Jej stworzenie jest banalnie proste – polega na naniesieniu poszczególnych ryzyk na wykres XY, gdzie współrzędnym X odpowiadają wartości prawdopodobieństwa, a współrzędne Y to wartości wyrażające skutek. Po naniesieniu wspomnianych wartości progowych dla skutku i prawdopodobieństwa mapa ryzyka jest gotowa.
Jakie są etapy oceny ryzyka zawodowego?
- Zebranie informacji potrzebnych do przeprowadzenia oceny ryzyka zawodowego.
- Identyfikacja zagrożeń. …
- Oszacowanie ryzyka.
- Określenie działań eliminujących lub ograniczających ryzyko zawodowe.
- Dokumentowanie wyników oceny ryzyka zawodowego.
Jak sporządzić ocenę ryzyka zawodowego?
Krok 1: Zidentyfikuj zagrożenia. Krok 2: Ustal, kto może ulec wypadkowi lub zachorować. Krok 3: Oszacuj ryzyko zawodowe wynikające z zagrożeń i oceń, czy zastosowane środki ochrony są właściwe oraz czy należy podjąć jeszcze jakieś działania w celu dalszego ograniczenia tego ryzyka. Krok 4: Udokumentuj wyniki.
Co należy zrobić gdy z oceny ryzyka wyjdzie ryzyko niedopuszczalne?
W sytuacji, gdy ryzyko jest niedopuszczalne, ograniczające je działania muszą być natychmiastowe, a praca musi być wstrzymana. Dopuszczalne średnie ryzyko wymaga prowadzenia takich działań, aby je zmniejszyć, ryzyko małe natomiast wymaga takich działań, które zapewnią, że pozostanie ono na tym samym poziomie.
Kto musi sporządzić ocenę ryzyka zawodowego?
Pracodawca jest osobą odpowiedzialną za dokonywanie oceny ryzyka zawodowego oraz o poinformowaniu pracowników o tym ryzyku, związanym z wykonywaną przez nich pracą. Za ocenę ryzyka zawodowego na poszczególnych stanowiskach pracy w firmie odpowiedzialny jest pracodawca.
Czy każdą maszyna musi mieć CE?
Każda maszyna wprowadzana do obrotu musi posiadać oznaczenie CE, które potwierdza spełnienia wszystkich wymagań dyrektywy 2006/42/WE. Dyrektywa w sprawie maszyn, dalej zwana dyrektywą maszynową (MD) została wprowadzona w Polsce Rozporządzeniem Ministra Gospodarki z dnia 21 października 2008 r.
Co oznacza CE na maszynie?
Zgodnie z r.z.w.m. za pomocą oznakowania CE producent informuje, że dany produkt spełnia zasadnicze wymagania i został poddany odpowiedniej procedurze oceny zgodności. Oznakowanie CE jest deklaracją producenta, że wytworzona przez niego maszyna spełnia określone w r.z.w.m. wymagania dotyczące danej maszyny.
Kiedy maszyna traci ce?
Zgodnie z założeniami Dyrektywy Maszynowej 2006/42/WE, jeżeli modyfikacje maszyny zostały przewidziane lub uzgodnione przez producenta i objęte oceną ryzyka, dokumentami i deklaracją zgodności WE producenta, pierwotne oznakowanie CE producenta zachowuje ważność.
Co to jest dyrektywa?
Dyrektywa jest aktem prawnym wyznaczającym cel, który muszą osiągnąć wszystkie państwa UE. Sposób jego osiągnięcia określają jednak poszczególne kraje za pośrednictwem swoich własnych aktów prawnych.
Czego dotyczy dyrektywa narzędziowa?
Dyrektywa dotyczy sposobu użytkowania sprzętu roboczego, tak więc wszelkiego rodzaju maszyny, narzędzia, osprzęt i instalacje techniczne , a także zgodnie z rozporządzeniem Ministra Gospodarki sprzęt do pracy na wysokości w szczególności drabiny i rusztowania.
Co to jest maszyną?
Maszyna – w najogólniejszym znaczeniu cybernetycznym – wszelki układ względnie odosobniony, w jakim zachodzi przekształcanie (transformacja) zasilenia lub informacji. Określenie to obejmuje zarówno układy fizyczne naturalne (w tym organizmy żywe), jak i urządzenia techniczne oraz pewne obiekty abstrakcyjne.
Która z procedur postępowania z wyrobem znajduje się w Dyrektywie Maszynowej?
Jednym z wymagań zawartych w dyrektywie w sprawie zasadniczych wymagań dla maszyn 2006/42/WE jest zastosowanie procedury oceny zgodności. Dzięki ich wykorzystaniu możliwe jest poprawne nadanie oznaczenia CE i wystawianie deklaracji zgodności WE na maszynę.
Bezpieczeństwo w systemach sterowania
Wg dyrektywy maszynowej 2006/42/WE, producent maszyny lub jego upoważniony przedstawiciel musi zapewnić przeprowadzenie oceny ryzyka w celu określenia wymagań w zakresie ochrony zdrowia i bezpieczeństwa, które mają zastosowanie do maszyny.
Zatem maszyna musi być zaprojektowana i wykonana z uwzględnieniem wyników oceny ryzyka. Za pomocą iteracyjnego procesu oceny ryzyka i zmniejszania ryzyka, producent lub jego upoważniony przedstawiciel:
określa ograniczenia dotyczące maszyny, w tym zamierzonego używania i możliwego do przewidzenia w uzasadniony sposób niewłaściwego jej użycia,
określa zagrożenia, jakie może stwarzać maszyna i związane z tym niebezpieczne sytuacje,
szacuje ryzyko, biorąc pod uwagę stopień możliwych obrażeń lub uszczerbku na zdrowiu i prawdopodobieństwo ich wystąpienia,
ocenia ryzyko, mając na celu ustalenie czy wymagane jest zmniejszenie ryzyka, zgodnie z celem niniejszej dyrektywy,
eliminuje zagrożenia lub zmniejsza ryzyko związane z takimi zagrożeniami poprzez zastosowanie środków ochronnych, zgodnie z hierarchią ważności ustanowioną w sekcji 1.1.2.b) dyrektywy maszynowej.
Aby maszyna została zaprojektowana i wykonana z uwzględnieniem wyników oceny ryzyka, ocena ryzyka musi zostać wykonana przed zaprojektowaniem maszyny. W procesie projektowania i budowy może jednak dojść do zmian konstrukcyjnych maszyny, więc w trakcie powstawania maszyny należy zapewnić odpowiedni sposób zarządzania ryzykiem, aby zapewnić zamierzony poziom bezpieczeństwa maszyny, zgodnie z aktualnym stanem wiedzy techniki.
Co to jest ryzyko?
Aby posługiwać się znaczeniem, które będzie rozumiane jednoznacznie, standardy wprowadzają definicje znaczeń dla słów rozumianych potocznie. Należało zatem zdefiniować znaczenie pojęcia ryzyka, aby skutecznie je zidentyfikować w celu określenia metod postępowania z ryzykiem. Jak się okazało, nie było to takie proste.
Wg dyrektywy 2006/42/WE ryzyko oznacza kombinację prawdopodobieństwa i stopnia obrażeń lub uszczerbku na zdrowiu, które mogą zaistnieć w sytuacjach niebezpiecznych.
Wg nieaktualnej już normy PN-EN 292-1, ryzyko to kombinacja prawdopodobieństwa wystąpienia urazu lub pogorszenia stanu zdrowia i stopnia ich ciężkości w sytuacji zagrożenia.
Wg norm serii PN 18000 jest to kombinacja częstości lub prawdopodobieństwa wystąpienia określonego zdarzenia wywołującego zagrożenie i konsekwencji związanych z tym zdarzeniem. Wg tej definicji, to nie zagrożenia powodują niepożądane zdarzenia, lecz odwrotnie – zdarzenia są źródłem zagrożeń. Wobec tego należałoby przyjąć, że w ogóle nie ma obiektywnych zagrożeń, jeśli coś złego się nie wydarzy.
Aktualna definicja ryzyka pojawiła się już w nieaktualnej normie PN-EN 1050 i w tej samej postaci funkcjonuje do dziś w normie PN-EN ISO 12100. Definicja ryzyka brzmi następująco:
Jak się zaraz okaże, definicja ryzyka nie jest czymś zupełnie nowym. Ryzyko to zjawisko, które dotyczy wszystkich organizmów żywych od początków istnienia życia. Wyobraźmy sobie satyryczną sytuację przedstawioną na obrazku poniżej. Bardzo lubię ten przykład i nie mogłem się powstrzymać od tego, aby go przedstawić 🙂
Aby przeżyć, pierwotny gatunek ludzki musiał polować. Aby zaspokoić potrzeby plemienia, człowiek pierwotny musiał podjąć ryzyko. Czynnikiem największego zagrożenia mogły być zwierzęta drapieżne, które mogły zapolować na człowieka. Mamy więc ryzyko i czynnik zagrożenia w postaci np. tygrysa szablastozębnego. Mamy również ciężkość szkody – upolowanie człowieka przez tygrysa szablastozębnego skutkuje w najgorszym wypadku śmiercią człowieka.
Czynnikiem zwiększającym prawdopodobieństwo wystąpienia zagrożenia jest współczynnik częstości narażenia na zagrożenie, a więc długotrwałe wędrówki w poszukiwaniu pożywienia i penetracja nieznanego terenu. Im dłużej trwa wędrówka człowieka pierwotnego, tym bardziej jest on narażony na niebezpieczeństwo. Mamy więc częstość i czas narażenia oraz prawdopodobieństwo wystąpienia zdarzenia zagrażającego.
Jeśli polowanie można zastąpić hodowlą zwierząt i uprawą roślin, zagrożenie można by całkowicie wyeliminować (często można się spotkać w normach o redukcji ryzyka “przez zastąpienie”). Jeśli jednak istnieje konieczność zapolowania na większe zwierzę, człowiek pierwotny mógł wytępić populację tygrysa, lub unikać spotkania z nim np. poprzez zwiady oraz informację o miejscu występowania. Mamy więc czynnik możliwości uniknięcia lub ograniczenia szkody i informacje na temat pozostałego ryzyka resztkowego po zastosowaniu wszelkich środków zaradczych.
Ryzyko nie jest zatem pojęciem wymyślonym, lecz zjawiskiem zupełnie naturalnym. Szacowanie i redukcja ryzyka pozwoliły człowiekowi przetrwać. Tygrys szablastozębny przegrał te walkę i nie przetrwał do naszych czasów. Definicja ryzyka w normach została przedstawiona w formie, która ma być wskazówką dla wyboru właściwej metodologii w szacowaniu, ocenianiu i eliminacji lub ograniczenia ryzyka na określone zdarzenie zagrażające. Zatem powinno się wybierać takie metody oceny ryzyka, które są najbardziej zbliżone do obowiązującej definicji ryzyka. A z tym jest zupełnie różnie. Norma PN-EN ISO 12100 nie narzuca metodologii.
Próbą uzupełnienia normy PN-EN ISO 12100 w tym zakresie jest raport techniczny ISO/TR 14121-2. Raport ten pojawił się dosyć późno w stosunku do obowiązujących wcześniej norm dotyczących oceny ryzyka, zharmonizowanych z dyrektywą maszynową.
Jakie metody oceny ryzyka są stosowane?
W latach, gdy obowiązywała stara dyrektywa maszynowa 98/37/WE, aktualny stan wiedzy na temat zasad oceny ryzyka był zawarty w normie PN-EN 1050. Metody oceny ryzyka były w tej normie opisane w sposób informacyjny w załączniku B. Były tam opisane jedynie niektóre z wielu istniejących metod analizy zagrożeń i szacowania ryzyka. Norma dopuszczała zastosowanie dwóch rodzajów metod analizy ryzyka:
metoda dedukcyjna – polegająca na przewidywaniu zdarzenia końcowego i poszukiwaniu zdarzeń, które do tego zdarzenia mogły doprowadzić;
– polegająca na przewidywaniu zdarzenia końcowego i poszukiwaniu zdarzeń, które do tego zdarzenia mogły doprowadzić; metoda indukcyjna – w której przewiduje się uszkodzenie elementu maszyny, a późniejsza analiza identyfikuje zdarzenia, które mogły być spowodowane tą awarią.
W normie PN-EN 1050 podane zostały przykładowe rodzaje metod dedukcyjnych i indukcyjnych, z krótką ich charakterystyką. Niektóre z tych metod zostały opisane w osobnych standardach. Norma PN-EN 1050, tak jak i zresztą PN-EN ISO 12100 nie narzucają stosowania konkretnej metody. Również raport techniczny ISO/TR 14121-2 tej kwestii nie precyzuje. W raporcie możemy przeczytać, że wybrana metoda lub narzędzie w dużej mierze będą zależały od preferencji branżowych, firmowych lub osobistych. Metody oceny ryzyka opisane w PN-EN 1050:
Wstępna analiza zagrożeń PHA;
Metoda „Co-gdy”;
Analiza rodzajów uszkodzeń i ich skutków FMEA;
Symulacja defektów w systemach sterowania;
Metoda systematycznej analizy ryzyka MOSAR;
Analiza drzewa błędów FTA;
Metoda DELPHI.
Nie będę tu szczegółowo opisywał wszystkich metod. Osoby zainteresowane znajdą więcej informacji na sieci. Nie wszystkie z powyższych metod można uznać za uniwersalne, nadające się do oceny ryzyka podczas projektowania maszyn z sektora maszynowego.
Po co stosuje się ocenę ryzyka?
Praktyka dotycząca budowy maszyn wskazuje ocenę ryzyka jako czynność, która ma zapewnić budowę bezpiecznych maszyn. Poprzez zastosowanie zasad bezpieczeństwa kompleksowego wg p. 1.1.2 dyrektywy maszynowej 2006/42/WE producent maszyny powinien wyeliminować lub ograniczyć ryzyko oraz poinformować o ryzyku resztkowym użytkownika maszyny. Wszystko po to, aby maszyna była na tyle bezpieczna, na ile zezwala na to aktualny stan wiedzy techniki dotyczący budowy maszyn. Szczegółowe informacje na ten temat można znaleźć w artykule “Projektowanie bezpiecznej maszyny”.
W jaki sposób przebiega ocena ryzyka?
Przy wybieraniu najwłaściwszych metod oceny i eliminacji lub redukcji ryzyka, producent lub jego upoważniony przedstawiciel musi stosować następujące zasady, według podanej kolejności:
wyeliminowanie lub zminimalizowanie ryzyka, tak dalece jak jest to możliwe (projektowanie i wykonywanie maszyn bezpiecznych z samego założenia,
podjęcie koniecznych środków ochronnych w związku z ryzykiem, którego nie można wyeliminować,
informowanie użytkowników o ryzyku resztkowym, spowodowanym jakimikolwiek brakami w przyjętych środkach ochronnych, wskazanie, czy konieczne jest szczególne przeszkolenie oraz określenie potrzeby stosowania środków ochrony osobistej.
Zasady te są znane szerzej w postaci tzw. triady bezpieczeństwa.
Krok 1 triady bezpieczeństwa – całkowicie bezpieczne działania projektowe: jeśli to możliwe, już konstrukcja samego wyrobu powinna eliminować zagrożenia (bezpieczeństwo budowy), np. unikanie zagrożeń lub redukcja ryzyka przez zmianę procesu produkcji, wybór właściwej technologii, zastąpienie pracy ręcznej przez proces kontrolowany automatycznie, zastąpienie niebezpiecznych (chemicznych) materiałów przez materiały bezpieczne itd. Eliminowanie zagrożeń poprzez projektowanie (stosowanie rozwiązań bezpieczeństwa opartych na stosowaniu rozwiązań bezpiecznych samych w sobie) jest najskuteczniejszą metodą ograniczania ryzyka, ponieważ usuwa źródło szkód.
Przykłady metod eliminowania zagrożeń:
całkowite wyeliminowanie zagrożenia na przykład poprzez zastąpienie łatwopalnej cieczy hydraulicznej cieczą niepalną;
projektowanie układów sterowania i elementów sterowniczych w celu zapewnienia bezpiecznego funkcjonowania;
zapewnienie stałej stateczności maszyny dzięki jej kształtowi i rozkładowi mas;
dopilnowanie, aby dostępne części maszyny nie miały ostrych krawędzi lub chropowatych powierzchni;
zapewnienie wystarczającej odległości między ruchomymi i stałymi częściami maszyny, aby uniknąć zagrożenia zgnieceniem;
unikanie sytuacji, w których dostępne powierzchnie będą miały ekstremalne temperatury;
zmniejszenie emisji hałasu, drgań, promieniowania lub substancji niebezpiecznych u źródła;
zmniejszenie, w miarę możliwości, prędkości i energii ruchomych części lub prędkości jazdy samej maszyny;
umiejscowienie niebezpiecznych części maszyny w niedostępnych miejscach;
umiejscowienie punktów regulacji i konserwacji poza strefami niebezpiecznymi;
eliminacja powtarzających się czynności i szkodliwych pozycji.
Krok 2 triady bezpieczeństwa – stosowanie technicznych środków bezpieczeństwa typu osłony i urządzenia ochronne: jeśli niemożliwa jest eliminacja najistotniejszych zagrożeń (lub ekonomicznie nieuzasadniona), ryzyko musi zostać zredukowane przez środki techniczne, takie jak stałe lub ruchome osłony, kabiny, obudowy. Jeżeli nie można wyeliminować zagrożeń lub odpowiednio zredukować ryzyko poprzez środki projektowe, powinno się zastosować techniczne środki ochronne (osłony i dodatkowe środki ochronne), które skutkują ograniczeniem narażenia na zagrożenia, obniżając prawdopodobieństwo niebezpiecznego zdarzenia lub poprawiając możliwości uniknięcia lub ograniczenia szkody.
Przykłady metod eliminowania zagrożeń:
stosowanie osłon stałych lub ogrodzenia w celu uniemożliwienia dostępu do stref zagrożenia;
stosowanie osłon ruchomych z ryglowaniem zapobiegających dostępowi do niebezpiecznych obszarów (np. urządzenia blokujące z ryglowaniem lub bez, klucze blokujące);
Stosowanie elektroczułego wyposażenia ochronnego do wykrywania osób wchodzących do, lub obecnych w strefie niebezpiecznej (na przykład kurtyny świetlne, maty czułe na nacisk);
Stosowanie urządzeń współpracujących z funkcjami bezpieczeństwa systemu sterowania maszyny (np. urządzenie zezwalające, urządzenie ograniczające sterowanie ruchem, urządzenie sterujące typu “przytrzymaj, aby uruchomić”);
Stosowanie urządzeń ograniczających (np. urządzenia ograniczające przeciążenia i moment, urządzenia do ograniczania ciśnienia lub temperatury, przełączniki nadmiernej prędkości, urządzenia do monitorowania emisji).
Jeśli środki bezpieczeństwa z zastosowaniem rozwiązań projektowych lub techniczne środki bezpieczeństwa nie spełniają celów ograniczenia ryzyka, można wykorzystać uzupełniające środki ochronne w celu osiągnięcia dalszej redukcji ryzyka.
Przykłady uzupełniających środków ochronnych których największym skutkiem jest zdolność unikania lub ograniczania szkód:
zatrzymanie awaryjne,
środki do uwalniania i ratowania osób uwięzionych,
środki zapewniające bezpieczny dostęp do maszyn,
przepisy dotyczące łatwego i bezpiecznego obchodzenia się z maszynami i ich ciężkimi częściami składowymi.
Należy jednak pamiętać, że uzupełniające środki ochronne nie mogą zastąpić technicznych środków ochronnych. Stosowanie uzupełniających środków ochronnych ma za zadanie uzupełnić funkcjonalność zastosowanych technicznych środków ochronnych w przypadku, gdy zastosowane środki okażą się niewystarczające, lub z analizy ryzyka wynika, że środki uzupełniające okażą się konieczne. Przykładem takiego uzupełniającego środka ochronnego może być przycisk zatrzymania awaryjnego umiejscowiony w strefie niebezpiecznej maszyny. Jeśli ocena ryzyka wykaże, że możliwe jest wejście człowieka do strefy niebezpiecznej, to zasadne może być wyposażenie strefy niebezpiecznej w dodatkowy środek ochronny w postaci takiego przycisku zatrzymania awaryjnego. Operator maszyny znajdujący się w środku może użyć takiego przycisku, gdy ktoś inny próbuje włączyć maszynę spoza strefy niebezpiecznej, np. z miejsca zainstalowania pulpitu sterowniczego, z którego widoczność wnętrza maszyny jest ograniczona.
Krok 3 triady bezpieczeństwa – redukcja zagrożeń z wykorzystaniem informacji dla użytkowników: zastosowanie piktogramów informujących o ryzyku resztkowym, środków ochrony indywidualnej (np. ubrań, osłon na oczy) itd. Dostawca powinien ostrzec użytkownika o ryzyku resztkowym, które pozostaje po redukcji ryzyka przez projektowanie i zastosowanie technicznych środków bezpieczeństwa. Informacje dla użytkownika obejmują:
informacje umieszczone na maszynie,
dokumentacja dostarczona z maszyną.
Informacje dla użytkownika dostarczone na maszynie obejmują:
znaki ostrzegawcze (piktogramy);
oznaczenia i etykiety do bezpiecznego stosowania (np. maksymalna prędkość obracających się części, maksymalne obciążenie robocze, dane dotyczące dostosowania osłon, kodowanie informacji kolorami);
sygnały dźwiękowe lub wizualne (np. sygnał dźwiękowy, dzwonki, gwizdki, światła);
inne urządzenia ostrzegawcze (na przykład bariery ostrzegawcze, wibracje).
Dokumentacja dostarczona z maszyną obejmuje:
podręczniki instruktażowe,
karty techniczne.
Dostawca powinien podać szczegóły w instrukcji obsługi na temat szkolenia, które jest niezbędne do zapewnienia prawidłowego wykorzystania z maszyny i zastosowanych środków ochronnych. Szkolenia mają głównie wpływ na zdolność jednostek do unikania szkód, a także może zmniejszyć narażenie i prawdopodobieństwo wystąpienia niebezpiecznego zdarzenia. Szkolenie i kompetencja są najważniejsze, gdy skuteczność środka ochronnego zależy od zachowania człowieka. Szkolenie powinno obejmować (ale nie ogranicza się do następujących):
informacje użytkowania dostarczone z maszyną;
informacje użytkowania opracowane przez użytkownika;
specjalistyczne szkolenia prowadzone przez dostawcę, jeśli są dostępne;
specjalistyczne szkolenia prowadzone przez użytkownika.
Kto wykonuje ocenę ryzyka?
Ocenę ryzyka wykonuje producent lub jego upoważniony przedstawiciel. Ocenę ryzyka można zlecić firmie specjalizującej się w takich tematach, należy jednak pamiętać w takich przypadkach o tym, że to producent lub jego upoważniony przedstawiciel będzie zawsze odpowiedzialny za ocenę ryzyka wykonaną przez osoby trzecie. Ocena ryzyka jest na ogół bardziej dokładna i skuteczna, gdy wykonuje ją zespół. Wielkość zespołu różni się w zależności od:
wybranego podejścia do oceny ryzyka;
złożoności maszyny;
procesu, w którym maszyna jest wykorzystywana;
Członkowie zespołu powinni być wybierani zgodnie z umiejętnościami i wiedzą wymaganą do oceny ryzyka. Zespół powinien obejmować tych ludzi, którzy:
mogą odpowiadać na pytania techniczne dotyczące konstrukcji i funkcji maszyny,
mają rzeczywiste doświadczenie w zakresie obsługi, ustawiania, konserwacji, serwisowania maszyn itp.,
posiadają wiedzę na temat historii wypadków podobnego typu maszyn,
dobrze rozumieją odpowiednie przepisy, normy, w szczególności normę PN-EN ISO 12100 i inne szczególne problemy bezpieczeństwa związane z maszyną, oraz
pojmują czynniki ludzkie mogące mieć wpływ na powstawanie zagrożeń.
Z oceną ryzyka jest zawsze taki problem, że stosując określoną metodę nie można zakładać, że każdy z zespołów jest w stanie dojść do tych samych wyników. Ale wiarygodność wyników oceny ryzyka jest tym większa, im większe jest doświadczenie zespołu integrującego osoby dysponujące wiedzą na temat różnych dyscyplin i różnorodnych doświadczeń i ekspertyzy. Doświadczenie wykazuje, że możliwe jest zawężenie wyników oceny ryzyka, przeprowadzanych przez różne zespoły, stosując dobrze opisaną metodę. Na potrzeby własne dobrze jest sprecyzować metodę tak, aby szczególnie podczas szeroko rozumianych pojęć “często” lub “rzadko”, sprecyzować te pojęcia, aby wynik oceny ryzyka nie zależał od rozmytej interpretacji tych pojęć.
Kontynuacja tego tematu jest dostępna w artykule “Jakie elementy powinna zawierać ocena ryzyka?”.
O OCENIE RYZYKA ZAWODOWEGO INFORMACJA WPROWADZAJĄCA
Ryzyko zawodowe to prawdopodobieństwo wystąpienia niepożądanych zdarzeń związanych z wykonywaną pracą powodujących straty, w szczególności wystąpienia u pracowników niekorzystnych skutków zdrowotnych w wyniku zagrożeń zawodowych występujących w środowisku pracy lub sposobu wykonywania pracy (Polska Norma PN-N-18002).
Ocenę ryzyka zawodowego można rozumieć jako dokładne sprawdzenie i ocenę, co w miejscu pracy może zaszkodzić lub wyrządzić krzywdę pracownikom. Dzięki niej można zweryfikować czy zastosowano wystarczające środki ograniczające lub eliminujące zagrożenia oraz określić, co należy jeszcze zrobić, aby do tego doprowadzić.
Ocena ryzyka prowadzi do upewnienia się, że prawdopodobieństwo, iż ktoś ulegnie wypadkowi lub zachoruje wskutek występowania zagrożeń w miejscu pracy, jest na możliwie najniższym poziomie. Ma to wpływ na “kondycję” przedsiębiorstwa bowiem wypadki przy pracy i choroby zawodowe negatywnie na nią wpływają m.in. poprzez zmniejszanie wydajności pracy i produkcji, opcję ponoszenia zwiększonej składki ubezpieczeniowej (kosztów ubezpieczenia), koszty ewentualnego uczestniczenia w postępowaniach sądowych, itd.
Najważniejsze jest jednak określenie jak znaczące zagrożenia występują w miejscu pracy i czy zapobiega się im przy pomocy właściwych i wystarczających środków zaradczych. Przykładowo: porażenie prądem elektrycznym może być śmiertelne, ale jego ryzyko jest bardzo małe w środowisku biurowym – oczywiście pod warunkiem, że elementy pod napięciem są dobrze izolowanie, a części metalowe dobrze uziemione.
Ocena ryzyka zawodowego, do której zobowiązany jest każdy pracodawca okazała się fundamentalnym narzędziem służącym bezpieczeństwu i zdrowiu pracowników w miejscu pracy, a jej regularne przeprowadzanie najprostszą drogą do stworzenia w przedsiębiorstwie bezpiecznych warunków pracy i kontrolowania stanu zagrożeń w miejscu pracy.
Ocena ryzyka zawodowego prowadzi do ochrony ludzkiego zdrowia i życia i służy oszczędzaniu pracownikom i pracodawcom stresu, strat finansowych i innych kłopotów związanych z ewentualnymi wypadkami przy pracy i chorobami zawodowymi.
Nie wymyślono nic bardziej logicznego i skutecznego, aby rozpoznać zagrożenia występujące na stanowiskach pracy, ocenić jakie mogą być ich konsekwencje dla bezpieczeństwa i zdrowia pracowników oraz określić możliwe środki przeciwdziałania tym zagrożeniom.
Z oceny ryzyka zawodowego wynika wiedza, na których stanowiskach pracy wykonywane są prace bezpieczne, a na których prace stwarzające zagrożenia (i jak poważne!) dla bezpieczeństwa i zdrowia pracowników.
Ocena ryzyka zawodowego to nie wymysł biurokracji ani zapisany w uregulowaniach prawnych formalny wymóg egzekwowany podczas kontroli przez Państwową Inspekcję Pracy, aby “utrudniać życie” pracodawcom. To podejście panujące we wszystkich krajach Unii Europejskiej, którego niezwykłą przydatność potwierdzają długoletnie doświadczenia “starych” krajów członkowskich Unii. To narzędzie wprowadzone do unijnego prawa już około 20 lat temu!
Praktyka “starych” państw członkowskich Unii Europejskiej dowiodła istnienia bezpośredniego związku między wynikami oceny ryzyka, a panującymi w przedsiębiorstwach warunkami pracy. Tam już dawno zauważono, że stałe zaangażowanie pracodawców i pracowników w prawidłową ocenę ryzyka prowadzi do powstania logicznie działającego systemu bezpieczeństwa pracy i przekonania, że dbanie o bezpieczeństwo i zdrowie to wspólny interes i zadanie zarówno dla pracodawców jak i pracowników.
Przeprowadzając ocenę ryzyka można liczyć na korzyści dla firmy. W bliższej perspektywie oznacza to lepsze samopoczucie pracowników i lepszą atmosferę w pracy, gdy pracodawca dba o ich bezpieczeństwo i zdrowie. Pracodawca natomiast może mieć świadomość spełnienia obowiązku o podstawowym znaczeniu dla ochrony zdrowia pracowników i zapobiegania ludzkiemu cierpieniu w jego firmie.
Ocena ryzyka zawodowego to działanie bardzo “na czasie” we wszystkich państwach członkowskich Unii Europejskiej. Zagadnieniem tym zajmuje się, w sposób szczególny, w formie europejskiej kampanii na rzecz oceny ryzyka zawodowego, unijna Europejska Agencja Bezpieczeństwa i Zdrowia w Pracy, a w Polsce Państwowa Inspekcja Pracy i Centralny Instytut Ochrony Pracy – Państwowy Instytut Badawczy. Dla pracodawców oznacza to łatwy dostęp do nowych, prostych, praktycznych i “inspirujących” materiałów pomocniczych, takich jak na przykład przejrzyste poradniki do oceny ryzyka lub łatwe do wykorzystania listy kontrolne do identyfikacji zagrożeń.
Ocenę ryzyka zawodowego można, a nawet zaleca się przeprowadzać w możliwie najprostszy sposób, a określenie zagrożeń i ocena związanego z nimi ryzyka powinny opierać się na zasadach zdrowego rozsądku. Może to zrobić sam pracodawca, mogą mu w tym pomóc kompetentni pracownicy lub ekspert spoza przedsiębiorstwa.
WSZYSTO JUŻ BYŁO, CZYLI JAK POMOCNA JEST PRAKTYKA I DOŚWIADCZENIE ŻYCIOWE?
Tak naprawdę każdy z nas już nieraz korzystał z efektów oceny ryzyka przeprowadzonej przez innych, a nawet sam ją przeprowadził np. w swoim domu! Dotyczy to także podjętych w jej następstwie działań ograniczających lub eliminujących ryzyko!
Przykładowo: już projektant zadbał, aby w Twojej łazience nie było włączników elektrycznych, elektryk zamontował kilka gniazdek “bezpiecznych dla dzieci” (z zamykaną klapką lub z przesłoną otworów), gazownik co roku sprawdza szczelność przewodów gazowych oraz drożność i sprawność przewodów wentylacyjnych. Czasem doradza Ci zmianę piecyka gazowego na bezpieczniejszy (samowyłączający się w przypadku uwalniania się tlenku węgla).
Występujące w tych przypadkach zagrożenia stwarzają duże ryzyko tragedii. Po przeczytaniu na ulotce, że zakupiony lek powinien być niedostępny dla dzieci, nie zostawia się go na stole tylko chowa do wyżej zawieszonej szafki, najlepiej dodatkowo zamykanej na klucz.
To samo dotyczy innych stwarzających zagrożenie przedmiotów, np. noży kuchennych, ostrych przedmiotów itd.. Małych dzieci nie zostawia się samych w domu. Ryzyko byłoby niedopuszczalne.
To ze względów bezpieczeństwa tabletki leków produkowane są w różnych kolorach, wielkościach i kształtach. Osoba przyjmująca różne leki nie pomyli się w ich dawkowaniu zgodnie z zaleceniem lekarza, np. nie weźmie dwóch takich samych tabletek, jeśli tego nie zlecił lekarz.
Nie przechowuje się (w jednej szufladzie) przypraw czy innych produktów żywnościowych razem z przydatnymi w domu artykułami chemii gospodarczej (np. klejami, środkami czyszczącymi itd.). Po co ryzykować pomyłkę, której konsekwencje mogłyby być tragiczne. Coraz częściej używając takich artykułów korzysta się z gumowych rękawic dla ochrony skóry rąk.
W łazienkach wykorzystuje się elementy antypoślizgowe (w wannie lub na zewnątrz) w obawie przed urazem. Czasami słyszy się o takich przypadkach lub samemu ich doświadcza. Jest to szczególnie ważne w przypadku ludzi starszych (osteoporoza). Dla nich ryzyko urazu jest jeszcze większe.
Nie umieszcza się ciężkich przedmiotów (które łatwo mogą spaść) na półkach zawieszanych nad miejscami do spania (jeśli w ogóle zawiesza się półki w takim miejscu). Po co ryzykować? I tak dalej, i tak dalej.
Każdy z nas mógłby podać wiele dalszych tego rodzaju przykładów, świadczących o tym, że mamy naturalny instynkt samozachowawczy, że potrafimy identyfikować zagrożenia, że potrafimy oceniać związane z nimi ryzyko i podejmować działania, które mają nas chronić przed potencjalnym nieszczęściem lub wypadkiem.
Wystarczy przenieść taką samą “filozofię” na grunt pracy zawodowej – dla dobra pracowników i pracodawców.
ILUSTRACJA PODSTAWOWYCH POJĘĆ NA PRZYKŁADZIE
JAZDY SAMOCHODEM
Ryzyko można określić jako iloczyn prawdopodobieństwa wystąpienia niepożądanego zdarzenia (np. wypadku samochodowego) związanego z wykonywaną czynnością i możliwych konsekwencji (skutków) tego zdarzenia (np. uszkodzenia samochodu lub urazu).
Prawdopodobieństwo jest definiowane jako częstotliwość wystąpienia niebezpiecznego zdarzenia w określonym okresie czasu. Przykładowo – jak często samochód może uczestniczyć w wypadku na głównej ulicy miasta w okresie rocznym? Czy jest to prawdopodobne, możliwe czy mało prawdopodobne?
Konsekwencje (skutki) zdarzenia to możliwe jego następstwa. Przykładowo – kolizja z udziałem szybko poruszającego się samochodu prawie zawsze pociąga za sobą jego poważne uszkodzenia i urazy lub śmierć osób biorących udział w wypadku.
Zagrożenie to obiekt, efekt fizyczny lub warunki mogące potencjalnie doprowadzić do uszkodzeń i obrażeń ciała u kierowcy, jego pasażerów, innych użytkowników drogi oraz do uszkodzeń samochodu.
Prowadzenie samochodu jest czynnością niebezpieczną, tym bardziej im większa jest jego prędkość. W przypadku prowadzenia samochodu można zidentyfikować następujące zagrożenia:
osoby przechodzące lub przebiegający przez drogę,
inni użytkownicy drogi zmieniający nagle pas jazdy,
samochody z przodu, które mogą nagle zahamować,
samochody z tyłu mogące przyśpieszyć lub niezwracające uwagi na czerwone światła,
niesprawność samochodu, – brudne szyby i lusterka,
niedyspozycja kierowcy (zmęczenie, wpływ alkoholu lub leków),
trudne uwarunkowania atmosferyczne.
Ograniczenie ryzyka wypadku samochodowego
Nikt nie chce polegać jedynie na tzw. łucie szczęścia, aby chronić się przed wypadkiem drogowym. Wykonuje się wiele czynności dla zmniejszenia ryzyka takiego wypadku, np.:
uczestniczy się w kursie na prawo jazdy i zdaje stosowny egzamin,
zapewnia się, że samochód jest w dobrym stanie (sprawne hamulce, bezpieczne opony), a szyby i lusterka są czyste,
dba się o zdolność do bezpiecznej jazdy (żadnego alkoholu, zakazanych lekarstw czy prowadzenia samochodu gdy jest się zmęczonym lub śpiącym),
zapina się pasy bezpieczeństwa (upewniając się, że to samo zrobili pasażerowie pojazdu, coraz częściej także na tylnych siedzeniach),
unika się jazdy w niesprzyjających warunkach atmosferycznych,
na dłuższych dystansach robi się okresowe przerwy w prowadzeniu samochodu i odpoczywa się,
przestrzega się ograniczeń prędkości, unika niebezpiecznego wyprzedzania (np. “na trzeciego”) itp.
Wszystkie wymienione wyżej środki to środki o charakterze prewencyjnym, które prowadzą do zmniejszenia ryzyka wypadku (odniesienia urazów, śmierci, uszkodzenia samochodu).
Ograniczenie konsekwencji wypadku samochodowego
Przykładowo: kierowca i pasażer samochodu jadącego z prędkością trzydziestu paru kilometrów na godzinę, po jego kolizji z samochodem stojącym na poboczu, nie poniosą żadnych lub nieznaczne urazy – dzięki temu, ze mieli zapięte pasy bezpieczeństwa. Jeśli natomiast dojdzie do wypadku, w którym kierowca poniesie poważne urazy, to ich konsekwencje mogą zostać ograniczone np. dzięki sprawnemu funkcjonowaniu służby zdrowia – szybki przyjazd karetki pogotowia ratunkowego i szybkie udzielenie fachowej pomocy medycznej mogą nawet uratować życie.
Zasadniczo wszelka działalność człowieka wiąże się dla niego z pewnym ryzykiem – występują zagrożenia, których nie zawsze można uniknąć, ale którym można przeciwdziałać.
ULOTKA INFORMACYJNA
“Ocena ryzyka zawodowego w małych przedsiębiorstwach”
Poniżej zamieszczono internetową wersję Ulotki informacyjnej, rozpowszechnianej w ramach kampanii informacyjno-promocyjnej na rzecz oceny ryzyka zawodowego (prowadzonej w latach 2008-2009 we wszystkich krajach UE), zawierającej przystępne wprowadzenie do problematyki oceny ryzyka zawodowego, zasady oceny ryzyka w pięciu krokach i szacowania ryzyka. Skorzystanie z podanego na końcu ulotki adresu internetowego Państwowej Inspekcji Pracy, zapewni osobom zainteresowanym szybki dostęp do prostych, “dydaktycznych” i ilustrowanych przykładami materiałów pomocniczych do oceny ryzyka, pochodzących z różnych źródeł (z podstrony “Oceny ryzyka zawodowego w małych przedsiębiorstwach”).
Zalecana literatura
1. I. Romanowska-Słomka, A. Słomka, Zarządzanie ryzykiem zawodowym, Tarbonus, 2007,
2. I. Romanowska-Słomka, Ryzyko zawodowe. Materiał szkoleniowy, wyd. PIP, 2002,
3. W. M. Zawieska (red.), Ryzyko zawodowe. Metodyczne podstawy oceny, wyd. CIOP, 2007,
4. I. Romanowska-Słomka, A. Słomka, Karty oceny ryzyka zawodowego dla 100 stanowisk pracy, wyd. SIGMA-Not, 2008,
5. Polska Norma PN-N-18002, Systemy zarządzania bezpieczeństwem i higieną pracy. Ogólne wytyczne do oceny ryzyka zawodowego.
Bezpieczeństwo w systemach sterowania
Dyrektywa maszynowa stanowi zbiór wymagań zasadniczych stawianych producentom maszyn.
Producent musi zapewnić, że maszyna wprowadzona po raz pierwszy na rynek Europejskiego Obszaru Gospodarczego (EOG) spełnia wymagania zasadnicze opisane w dyrektywie maszynowej 2006/42/WE.
Dyrektywa maszynowa mieści się w zbiorze dyrektyw tzw. “nowego i globalnego podejścia” dotyczących projektowania, budowy i wprowadzania na rynek wyrobów, wydawanych w celu zapewnienia możliwie najwyższego poziomu ich bezpieczeństwa. Tylko wyroby spełniające wymagania ujęte w tych dyrektywach mają zapewniony swobodny przepływ w Europejskim Obszarze Gospodarczym.
W dyrektywie maszynowej podano definicje maszyny, a obowiązkiem producenta jest określenie, na podstawie tych definicji, czy jego produkt podlega dyrektywie. Zdefiniowano pojęcie maszyny w sensie ogólnym, zespół maszyn, sprzęt wymienny oraz urządzenie zabezpieczające. Wykluczono z zakresu dyrektywy takie wyroby, jak: maszyny, których jedynym źródłem napędu jest siła mięśni ludzkich, z wyjątkiem maszyn używanych do podnoszenia i opuszczania ładunków,
maszyny do użytku medycznego mające bezpośredni kontakt z pacjentem,
kotły parowe, zbiorniki i zbiorniki ciśnieniowe,
broń palna,
różnego rodzaju dźwigi,
oraz wiele innych.
Treść dyrektywy można pobrac stąd: link
8 kroków do bezpiecznej maszyny – Od oceny ryzyka do oznaczenia CE
8 kroków do bezpiecznej maszyny – Od oceny ryzyka do oznaczenia CE Producenci maszyn są zobowiązani do przeprowadzenia procedury oceny zgodności swoich maszyn. Poprzez umieszczenie znaku CE producent potwierdza, że urządzenie lub maszyna spełnia wszystkie zasadnicze wymagania dyrektywy maszynowej 2006/42/WE dotyczące zdrowia i bezpieczeństwa. Do pokonania tej drogi potrzeba 8 kroków. W obrębie UE, punktem odniesienia dla bezpieczeństwa maszyn i urządzeń jest Dyrektywa Maszynowa. Określa ona znormalizowany poziom bezpieczeństwa, gwarantujący swobodny przepływ towarów.
Krok 1: Ocena ryzyka jako klucz do bezpieczeństwa maszyn
Producenci maszyn działający na wewnętrznym rynku europejskim są zobowiązani dostarczać do klientów wyłącznie produkty bezpieczne. Zatem zgodnie z warunkami Dyrektywy Maszynowej, producent maszyny musi przeprowadzić ocenę ryzyka. Taka ocena ryzyka powinna zawierać identyfikację obowiązujących norm i przepisów zharmonizowanych, określenie ograniczeń maszyny, identyfikację wszystkich zagrożeń w każdej z faz cyklu życia maszyny, rzeczywiste oszacowanie i ocenę ryzyka, a także zalecane podejście w celu zmniejszenia ryzyka.
Poziom ryzyka obliczany jest na podstawie prawdopodobieństwa wystąpienia oraz potencjalnej powagi obrażenia.
Krok 2: Opracowanie koncepcji bezpieczeństwa
Pojęcie koncepcji bezpieczeństwa określa środki techniczne oraz gwarantuje bezpieczeństwo Twojej maszyny zgodnie z krajowymi i międzynarodowymi normami zharmonizowanymi. Dobra koncepcja bezpieczeństwa rozwiąże powtarzający się konflikt, który powstaje pomiędzy zabezpieczeniami i wydajnością produkcji.
Koncepcja bezpieczeństwa uwzględnia na przykład wykorzystanie stałych i mobilnych zabezpieczeń, systemów do zatrzymania maszyn i urządzeń, opcji bezpiecznego wyłączenia energii elektrycznej, jak również cieczy i gazów pod ciśnieniem oraz wykrywanie pracowników w strefach niebezpiecznych.
Krok 3: Projektowanie układów bezpieczeństwa i dobór komponentów bezpieczeństwa
Celem projektu bezpieczeństwa jest zmniejszenie lub wyeliminowanie niebezpiecznych punktów, poprzez szczegółowe planowanie niezbędnych środków ochronnych. Dotyczy tego, czy maszyna ma być zbudowana od nowa, zmodernizowana czy przerobiona. W szczególności dotyczy to projektowania systemów mechaniki, elektryki, elektroniki, oprogramowania i systemów sterowania, a także doboru komponentów.
Krok 4: Prawidłowy dobór elementów bezpieczeństwa
W celu doboru odpowiednich komponentów, należy koniecznie ustalić i zweryfikować Poziom Zapewnienia Bezpieczeństwa (Performance Level – PLr) lub Poziom Nienaruszalności Bezpieczeństwa (Safety Integrity Level – SIL), który ma być osiągnięty zgodnie z EN ISO 13849-1 / EN IEC 62061. Wsparcie dla tej skomplikowanej procedury zapewniają odpowiednie narzędzia obliczeniowe. Na podstawie wartości charakterystycznych zaplanowanych lub używanych elementów związanych z bezpieczeństwem, Kalkulator Bezpieczeństwa PASCAL firmy Pilz potwierdza uzyskane wartości, w tym wymaganych lub pożądanych wartości domyślnych PLr lub SIL. Zaletą narzędzi programowych jest to, że przeprowadzają krok po kroku przez poszczególne etapy, uczestniczące w walidacji funkcji bezpieczeństwa.
Krok 5: Integracja systemu
Wybrane środki bezpieczeństwa realizowane są w oparciu o wyniki oceny ryzyka i koncepcji bezpieczeństwa. Całość obejmuje wybór odpowiednich dostawców, zakup komponentów i wdrożenie rozwiązań systemowych, konfigurację systemów sterowania i tworzenia interfejsów wizualizacji, instalację elektrycznych maszyn i urządzeń, montaż mechanicznych środków ochronnych i elementów hydraulicznych, montaż i testowanie szaf sterowniczych oraz szkolenie operatorów maszyn i pracowników obsługi technicznej.
Krok 6: Ponowna oceny ryzyka
Ponowna ocena ryzyka analizuje kroki podjęte wcześniej: Czy środki ochronne zostały wprowadzone prawidłowo? Czy bezpieczeństwo zostało prawidłowo zaprojektowane w powiązaniu z systemem sterowania maszyny i czy zostało ono zrealizowane zgodnie z przepisami bezpieczeństwa? Walidacja jest niezbędna do udowodnienia, że maszyny są bezpieczne. Ponowna ocena ryzyka obejmuje również testowanie działania oraz symulację usterek w systemie bezpieczeństwa, jak również różne pomiary (przewód ochronnych, emisji hałasu, …). Wyniki są rejestrowane i dokumentowane.
Krok 7: Instrukcje obsługi
Podczas dostawy urządzeń, maszyn i produktów, instrukcja obsługi jest jej integralnym składnikiem. Jeśli błąd prowadzi do wypadku, wówczas każda pomyłka w instrukcji obsługi może mieć konsekwencje prawne.
Wskazówki dotyczące bezpieczeństwa są kluczowym elementem wszystkich instrukcji. Według ustawodawcy, muszą opisywać całe ryzyko resztkowe od zagrożeń, jakie pozostały po zastosowaniu środków ochronnych. Konstruktorzy maszyn muszą również brać pod uwagę ryzyko, jakie może powstać po stronie użytkownika przy każdym, “możliwym do przewidzenia niewłaściwym użyciu” maszyny. Więc uważna ocena ryzyka jest podstawą do opracowania instrukcji obsługi.
Krok 8: Certyfikat CE
Producent lub osoba wprowadzająca produkt na rynek, dołączając znak CE do swojego produktu ostatecznie potwierdza, że jego produkt spełnia wszystkie wymagania prawne Dyrektywy Maszynowej 2006/42/WE oraz spełnia warunki w zakresie zapewnienia jego właściwości, w przypadku gdy produkt używany jest zgodnie ze swoim przeznaczeniem. Dla wszystkich maszyny importowanych z krajów spoza UE, niezależnie od roku produkcji, również wymagany jest znak CE. Dołączanie znaku CE jest wyłączną odpowiedzialnością producenta lub osoby wprowadzającej produkt na rynek i nie wymaga żadnego oficjalnego zatwierdzenia.
Jeśli pojedyncze maszyny, które posiadają już certyfikat CE, są ze sobą połączone tworząc zespół maszyn (instalację), procedura oceny zgodności, w tym oznakowania CE należy przeprowadzić dla całej instalacji.
Ocena ryzyka maszyn
Połączenie prawnych i indywidualnych wymagań
W celu wykonania oceny ryzyka operatorzy i producenci maszyn potrzebują koncepcji, która spełnia wymagania przepisów krajowych oraz międzynarodowych dyrektyw i norm. Aby to osiągnąć, potrzebna jest praktyczna, usystematyzowana i nastawiona na konkretny cel ocena instalacji i maszyn.
Od samego początku po Twojej stronie
Nasi doświadczeni specjaliści opracowują podstawy oceny ryzyka, która będzie dostosowana do Twoich konkretnych wymagań. Zawsze działamy zgodnie z polityką firmy klienta, jej wewnętrznymi procedurami i wymaganiami.
ocena ryzyka maszyny wg dyrektywy MAD 2006/42/WE
Ta strona korzysta z plików cookie, aby poprawić komfort użytkowania. Zakładamy, że nie masz nic przeciwko, ale możesz zrezygnować, jeśli chcesz. więcej AKCEPTUJĘ
Analiza, ocena i ewaluacja ryzyka maszyn
Dyrektywa 2009/104/WE
Maszyny eksploatowane i wyprodukowane przed 2004, nie posiadające oznaczenia CE na tabliczce znamionowej, powinny zostać tak zmodernizowane, by spełnić minimalne wymagania techniczne określone w dyrektywie narzędziowej 2009/104/WE.
Dyrektywa narzędziowa odnosi się do obecnie eksploatujących maszyny wyprodukowane przed 2004 rokiem, podmiotów gospodarczych, zakładów pracy itp. i nakłada na nich obowiązek ew. modernizacji maszyn celem spełnienia wymagań minimalnych.
Po bezpiecznej stronie, czyli jak oszacować ryzyko funkcjonowania maszyny
Po bezpiecznej stronie, czyli jak oszacować ryzyko funkcjonowania maszyny
Maszyny i kompleksowe systemy stworzone dla konkretnej aplikacji powinny spełniać wszystkie założenia projektowe i wydajnościowe, ale także zapewnić bezawaryjną i bezpieczną pracę.
W Unii Europejskiej, czyli również w Polsce producentów maszyn obowiązuje Dyrektywa Maszynowa 2006/42/WE.
Poza tym mamy normy. Czym tak naprawdę one są? Czy mamy obowiązek je przestrzegać? Normy nie są aktami prawnymi, ponieważ nie są publikowane w dzienniku ustaw oraz nie są ogólnodostępne (musimy za nie zapłacić), więc nie mamy obowiązku ich przestrzegania. Czym więc są? Dla mnie są drogowskazami, które pomagają dotrzeć do celu, którym – w naszym przypadku – jest spełnienie założeń dyrektywy maszynowej, czyli wypuszczenia na rynek maszyny bezpiecznej dla użytkowników.
Norm mamy tysiące i odnoszą się tak naprawdę do wszystkiego. Jest jednak prosty sposób na dotarcie do tych, które w obecnej chwili nas interesują (np. dotyczą konkretnego typu maszyn) oraz są aktualne. Trzeba zapoznać się z normami zharmonizowanymi oraz listami norm zharmonizowanych z daną dyrektywą.
I właśnie na liście norm zharmonizowanych z dyrektywą maszynową znajduje się sławna norma ISO 13849 – Bezpieczeństwo maszyn – Elementy systemów sterowania związane z bezpieczeństwem – Część 1: Ogólne zasady projektowania, której obecne (25.08.2016) zharmonizowane wydanie ma nr PN-EN ISO 13849-1:2016-02. Wprowadza ona pojęcia kategorii bezpieczeństwa (PL), współczynniki MTTF, DC, CCF – ale o tym, kiedy indziej.
Dzisiaj skupimy się zupełnie na czym innym, na chwilę zapominamy o normie ISO 13849 i zaczynamy temat bezpieczeństwa „od początku”. Inżynieria bezpieczeństwa powinna zacząć się już na etapie projektowania układu. Niestety, bardzo często bezpieczeństwem zajmujemy się na samym końcu, co zwykle wiąże się z dodatkowymi kosztami.
Tak prawidłowo powinien wyglądać proces
A tak bardzo często wygląda
Postarajmy się ułożyć po kolei wszystkie elementy dotyczące zapewnienia bezpieczeństwa w naszej aplikacji.
Dzisiaj zajmiemy się 1 punktem, czyli oceną ryzyka. Wszystkie możliwe zagrożenia i scenariusze awarii, które mogą pojawić się w aplikacji powinny zostać przeanalizowane i poddane ocenie. Może nam w tym pomóc norma ISO 12100 (jest to również norma zharmonizowana z MD). W oparciu o otrzymane wyniki powinniśmy wyeliminować ryzyko. Jeżeli nie mryożna tego zrobić, to trzeba przynajmniej je ograniczyć. Musimy pamiętać, że analizie należy poddać wszystkie stany, w których może znaleźć się układ: tryb pracy automatycznej, tryb pracy ręcznej, konserwacji, czyszczenia itp.
Poniżej uproszczony schemat oceny ryzyka wg ISO 12100
Przeanalizujmy pierwszą część schematu, zaczynając od określenie ograniczeń maszyny i jej właściwego użytkowania.
W tym miejscu powinniśmy dokładnie określić:
– do czego maszyna jest przeznaczona,
– w jakich warunkach będzie pracowała,
– jaka jest jej wydajność.
Wszystkie założenia poczynione na tym etapie będziemy musieli zawrzeć również w instrukcji obsługi. Pozwoli to nam to ograniczyć liczbę zagrożeń, które będziemy musieli uwzględnić w kolejnych krokach. Przykład: projektujemy maszynę, która zgodnie z założeniami ma pracować w hali produkcyjnej. Dzięki wpisaniu takiego ograniczenia w analizie ryzyka możemy pominąć zagrożenia związane np. z pracą maszyny na zewnątrz (zmienne warunki atmosferyczne). Zawarcie tej informacji w instrukcji obsługi zabezpieczy nas przed ewentualnymi konsekwencjami związanymi z niewłaściwym wykorzystaniem maszyny przez użytkownika.
Identyfikacja wszystkich zagrożeń
Po określeniu ograniczeń możemy przystąpić do identyfikacji zagrożeń. I znowu pomocna może być norma ISO 12100, w której znajdują się listy kontrolne ułatwiające identyfikację zagrożeń występujących przy obsłudze maszyn i urządzeń.
Analiza ryzyka dla każdego zagrożenia
Do analizy ryzyka stosuje się najczęściej metodę wykorzystującą dwa parametry ryzyka: ciężkości następstw (skutków) występujących w aplikacji zagrożeń oraz prawdopodobieństwa, z jakim następstwa te (urazy, choroby) mogą wystąpić.
Ryzyko = rozmiar szkód x prawdopodobieństwo wystąpienia
Oszacowanie ryzyka
Po zidentyfikowaniu oraz analizie zagrożeń należy przeprowadzić oszacowanie ryzyka dla każdej rozpatrywanej sytuacji niebezpiecznej. Istnieją różne narzędzia służące do oszacowania ryzyka, np. tabele, grafy ryzyka, metody numeryczne itp.
Podczas oceny ryzyka ustalamy, czy konieczne jest zastosowanie zmian konstrukcyjnych. Jeżeli zmiany konstrukcyjne są niemożliwe, zmniejszenie poziomu ryzyka realizuje się poprzez zastosowanie technicznych środków ochronnych. Proces oceny ryzyka jest iteracją, którą kończymy po osiągnięciu akceptowalnego poziomu ryzyka i nazywamy je ryzykiem resztkowym (szczątkowym). Informacja o ryzyku resztkowym powinna znaleźć się w instrukcji obsługi.
Na koniec tej części chciałby zwrócić uwagę na jeszcze jedną sprawę. Jak można zauważyć na schemacie oceny ryzyka, mamy rozgraniczone dwa aspekty związane ze zmniejszaniem poziomu ryzyka. Są to:
– zmiany konstrukcyjne – do których możemy zaliczyć odległości bezpieczne, minimalne odstępy zapobiegające zgnieceniu ciała
– techniczne środki ochronne – do których należą osłony, kurtyny świetlne, układy sterowania.
Więcej o poziomie ryzyka w kolejnym odcinku.
Tomasz Ciesielski, WAGO.PL
키워드에 대한 정보 przykładowa ocena ryzyka maszyny
다음은 Bing에서 przykładowa ocena ryzyka maszyny 주제에 대한 검색 결과입니다. 필요한 경우 더 읽을 수 있습니다.
이 기사는 인터넷의 다양한 출처에서 편집되었습니다. 이 기사가 유용했기를 바랍니다. 이 기사가 유용하다고 생각되면 공유하십시오. 매우 감사합니다!
사람들이 주제에 대해 자주 검색하는 키워드 Odc. 6: Procedura oceny zgodności – dokumentacja techniczna, ocena ryzyka, badania i testy
- 동영상
- 공유
- 카메라폰
- 동영상폰
- 무료
- 올리기
Odc. #6: #Procedura #oceny #zgodności #- #dokumentacja #techniczna, #ocena #ryzyka, #badania #i #testy
YouTube에서 przykładowa ocena ryzyka maszyny 주제의 다른 동영상 보기
주제에 대한 기사를 시청해 주셔서 감사합니다 Odc. 6: Procedura oceny zgodności – dokumentacja techniczna, ocena ryzyka, badania i testy | przykładowa ocena ryzyka maszyny, 이 기사가 유용하다고 생각되면 공유하십시오, 매우 감사합니다.